摘要 摘要:硬質(zhì)材料像高合金化高速鋼在磨削加工過程中出現(xiàn)的復(fù)雜熱機械載荷,會影響表面完整性進而影響工程零件的性能。殘留應(yīng)力則是評估磨削零件性能的一個顯著參數(shù)。早期研究指出磨削工藝通常就是...
作者:Haifa Sallen, Hedi Hamdi
摘要:硬質(zhì)材料像高合金化高速鋼在
磨削加工過程中出現(xiàn)的復(fù)雜熱機械載荷,會影響表面完整性進而影響工程零件的性能。殘留應(yīng)力則是評估磨削零件性能的一個顯著參數(shù)。早期研究指出磨削工藝通常就是工件的拉伸表面殘余應(yīng)力的來源。本研究中,通過x射線衍射對磨削工件的測量發(fā)現(xiàn)表面產(chǎn)生較大的壓縮殘余應(yīng)力。為理解該殘余應(yīng)力的來源,實驗建立了
外圓精磨有限元素模擬模型,且溫度取決于材料屬性;并采用SYSWELD 2010軟件根據(jù)二維數(shù)值模擬建立了熱機械模擬。利用工件表面移動的等量熱通量來模擬CBN
砂輪對工件的加工作用。根據(jù)實驗測量和分析計算求得熱源輪廓。將砂輪的機械作用模擬為分布在接觸區(qū)磨粒上的正常壓力。求得溫度分布和殘余應(yīng)力。模擬結(jié)果和測量結(jié)果之間的差別是比較明顯的。進一步對磨削表面層進行表征,發(fā)現(xiàn)在給定的工藝參數(shù)、砂輪和材料屬性條件下,等量載荷的熱機械模型不足以在塑性變形和結(jié)構(gòu)變化中再生誘導(dǎo)殘余應(yīng)力。
關(guān)鍵詞:磨削,殘余應(yīng)力,有限元素模型(FEM),表面結(jié)構(gòu)
1、引言
高合金化高速鋼(HSS)由于其碳化物和馬氏體基體的硬度非常高而被當作耐磨材料,并應(yīng)用在鋼材軋制等強力苛刻加工工藝的成形工序中。在加工前對這類機械零件的表面完整性進行一個預(yù)測可以保障加工過程的安全性和產(chǎn)品的質(zhì)量。表面完整性的主要指標有表面微結(jié)構(gòu)和殘余應(yīng)力等。本論文主要對
CBN砂輪對高速鋼進行外圓精磨加工時所產(chǎn)生的殘余應(yīng)力進行研究分析。
有研究者指出殘余應(yīng)力輪廓主要受最后的制造加工影響,而制造工序也是影響最終表面完整性的主要因素。磨削作為一種精確加工工藝,適宜高硬度終極精磨材料的加工。對于光滑表面和精準公差要求高的零部件加工,磨削是其工藝的最后關(guān)鍵一步。但大多數(shù)加工操作中由于碎屑形成機制的緣故,很大一部分能量被轉(zhuǎn)化為熱能并在
磨料-工件之間產(chǎn)生高溫;最終導(dǎo)致以表面軟化為形式的熱損傷、殘余應(yīng)力和再硬化。
在磨削工序中,砂輪類型、材料硬度和工藝參數(shù)等因素都會影響零件的應(yīng)力狀態(tài)。在砂輪類型方面,Kohli等人研究發(fā)現(xiàn)傳統(tǒng)
剛玉砂輪加工時傳遞到工件上的磨削能總量約有60-75%被轉(zhuǎn)化為磨削區(qū)的熱能;而CBN砂輪的這一數(shù)據(jù)約20%;所以使用CBN砂輪能夠降低熱損傷。
為研究工件磨削過程中殘余應(yīng)力的來源及其形式,實驗建立了FEA物理模擬。數(shù)值模擬需要對耦合現(xiàn)象的不同類型進行建模:熱力的、機械的和冶金的。一些研究者提出了不同的建模,其中考慮了部分或所有的以上現(xiàn)象。在最為普遍的FE模型中,工件上的移動熱源代表砂輪。因此,需要知道傳導(dǎo)入工件的熱通量密度。大多數(shù)溫度模型都根據(jù)Jaeger理論求得磨削工件上的溫度分布。但現(xiàn)有模型大多都忽略了砂輪的機械作用,在熱源的結(jié)構(gòu)影響方面有所局限。
本論文利用CBN砂輪對高速鋼進行外圓磨削加工,從而研究殘余應(yīng)力分布及其變化。通過等量熱源的耦合熱機械FE模型求得模擬實驗結(jié)果,將模擬結(jié)果與實驗實測結(jié)果進行對比。對比差異主要表現(xiàn)為較高的壓縮殘余應(yīng)力來源,特別是在低溫和高熱穩(wěn)固材料(HSS)的條件下。然后,通過次表面微結(jié)構(gòu)的詳細分析做進一步的完善。
2、實驗
2.1 實驗?zāi)ハ餮b置
本研究采用HERMLE CNC 5軸加工中心進行外圓外圍縱向精磨加工;所用CBN砂輪直徑Ds=150mm,寬度b=12mm;工件為硬鋼柱,直徑Dw=116mm、200mm,硬度為63HRC;設(shè)計定制特殊的噴嘴用于磨削區(qū)的油潤滑。整個實驗裝置如圖1所示。
圖一:實驗裝置
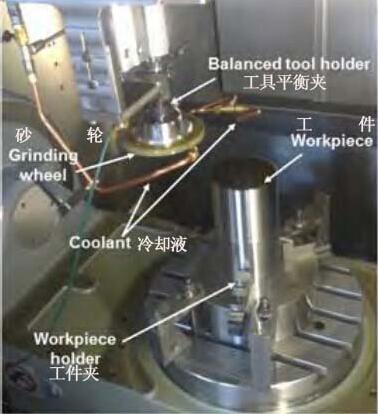
根據(jù)包含5個工藝參數(shù)和混合水準(兩到三個[32 23])的部分析因試驗設(shè)計進行實驗,共計36組實驗;加工方向為順磨、逆磨兩個方向;不同砂輪速度、工件速度、切割深度、進給速率和磨削防線。如表一所示。
表一:因子水準分配
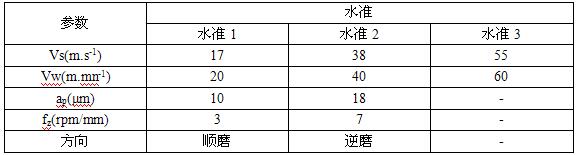
2.2 殘余應(yīng)力測量
每組實驗做完后,利用帶有鉻放射線 Cr Kα(λ=0.229mm)和一個3.14mm直徑的入射光束準直器的MGR40頭的PROTO X射線衍射進行殘余應(yīng)力測量,如圖2所示。對鐵板(211)的測量也用該裝置,Bragg’s角2θ=156.1°。以ψ正負值進行sin2ψ方法的測量:
6-ψ角度(-30°~+30°)
Ψ振蕩:±3°
對表面層進行持續(xù)的電溶解直至達到要求的深度后就可以實現(xiàn)徹底的殘余應(yīng)力分布。以兩個正交方向進行殘余應(yīng)力的測量:進給方向(σzz)和砂輪切削方向(σxx)。
圖二:X射線機進行殘余應(yīng)力測量
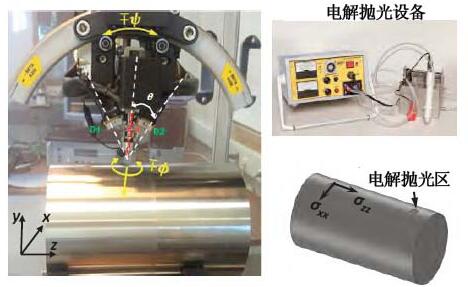
3、實驗結(jié)果
圖三為磨削加工前后工件的殘余應(yīng)力深度輪廓數(shù)據(jù)。由圖觀察可知,前期加工工藝所產(chǎn)生的拉伸表面殘余應(yīng)力在經(jīng)過磨削加工后,被轉(zhuǎn)化為最大表面壓縮應(yīng)力。
圖三:HSS外圓磨削前后的殘余應(yīng)力
根據(jù)參考文獻[20]對殘余應(yīng)力反映圖中實驗設(shè)計的分析可知,工件速度對磨削試樣上產(chǎn)生的殘余應(yīng)力的影響最大,其次是砂輪進給速度。圖4為順磨方向上不同工件速度(7、14、22m.min-1)和經(jīng)過修整的其他工藝參數(shù)條件(Vs=17m.s-1,fz=3mm.tr-1,ap=8μm)下求得的殘余應(yīng)力輪廓。在兩個方向上,殘余應(yīng)力是完全壓縮的。值得注意的是,位于外層的壓縮峰值在Vw=7m.m-1處最高且主要在切削方向上(4a)。進一步分析則會發(fā)現(xiàn),峰值之間的差異更顯著,工件速度對殘余應(yīng)力的影響表現(xiàn)在了磨削表面下方的受影響層上。工件速度越低,受影響深度就越大,從Vw=22m.min-1的10μm到Vw=7m.min-1的80μm。
圖四:不同工件速度條件下的殘余應(yīng)力輪廓
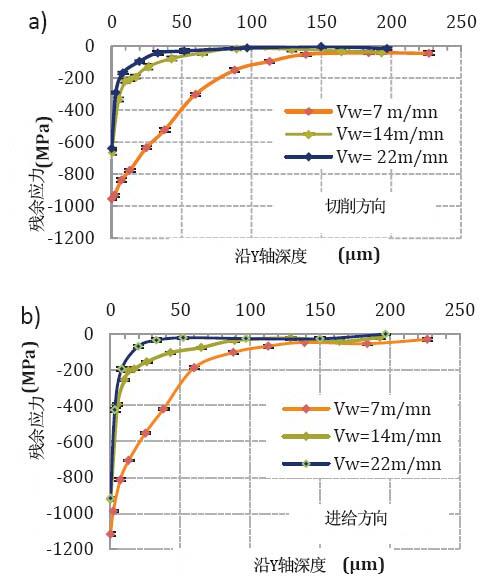
4、外援磨削加工后殘余應(yīng)力的計算模型
4.1 數(shù)字模型設(shè)計
數(shù)字模型主要用來模擬外圓精磨工藝中產(chǎn)生的殘余應(yīng)力,如圖5所示。所采用的方法并未考慮切屑去除機理。將砂輪假設(shè)為隨著工件速度Vw沿著表面移動的熱源。
圖五:數(shù)字模型:熱載荷和界面狀況
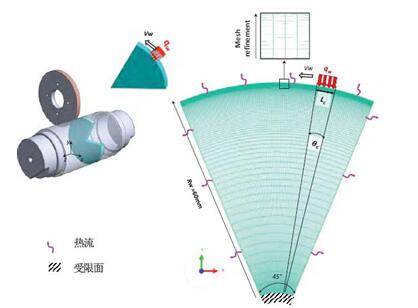
在砂輪的單圈加工過程中,沿表面的磨削條件在切削、進給兩個方向上保持常量,因此可以僅考慮柱工件的一部分即可。利用SYSWELD軟件對柱件的第8個2D平面應(yīng)變模型進行處理。在建立該2D模型時還要考慮不同溫度條件下的材料屬性。
工件的初始溫度T(t=0)=20℃。在上表面和側(cè)面,用熱對流傳導(dǎo)系數(shù)hconv(W.K-1.mm-2)來表示熱對流。底面的熱損失假定為0。熱邊界條件如圖五所示。
4.2 熱源求值
熱源長度和砂輪-工件之間的接觸長度相等。
進入工件的熱通量計算如下:
圖六:熱源計算
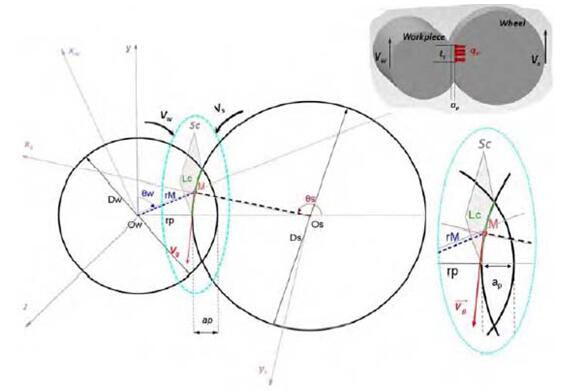
公式1為磨削過程中產(chǎn)生的總能量。Ft為磨削切向力,Vg為工件-砂輪滑動速度。此外,還觀察到在磨削中所有產(chǎn)生的能量都被轉(zhuǎn)化為熱能。砂輪-工件間的熱通量總量qT(W.mm-2)和公式4的滑動速度以及公式2中單位接觸面積ft(N.mm-2)上的切向磨削力成比例關(guān)系。
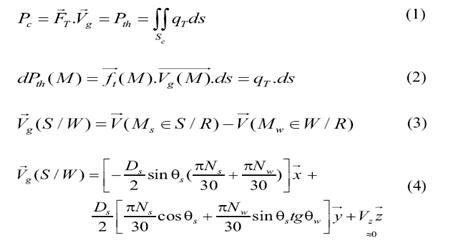
.
最后,工件qw(W/mm-2)上的熱通量密度計算如下: 其中, εw是轉(zhuǎn)化為工件上熱量的總能量的一部分。在CBN砂輪配用油潤滑加工中,εw約為20%。實驗發(fā)現(xiàn)在外圓精磨中,熱通量形狀為準矩形。
4.3 機械模型裝置
機械計算考慮了熱彈塑性機械性能;求得弱耦合熱機械計算。砂輪的影響模擬為速度為Vw沿著表面移動的正常壓力。外加荷載的量級由接觸區(qū)的正常磨削力求得。通過X、Y方向上對位移的限制求得工件底面上的運動學(xué)邊界條件。
4.4 熱學(xué)結(jié)果
圖七為模擬的熱學(xué)結(jié)果,條件參數(shù)為:Vw=7m.mn-1,Vs=17m.s-1,fz=3mm.tr-1,ap=8μm。
圖七:不同深度條件下沿切削方向的溫度輪廓
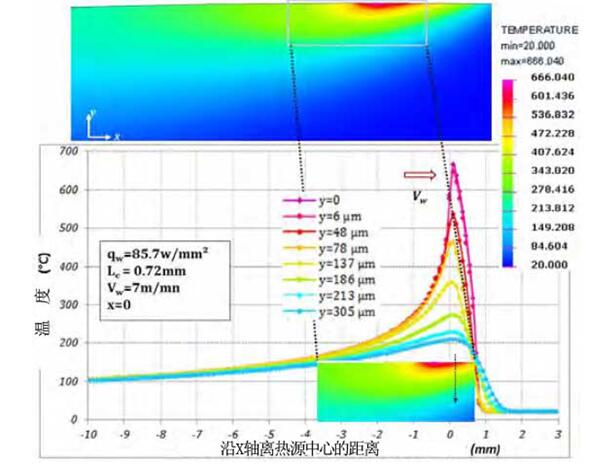
觀察發(fā)現(xiàn)最高峰值溫度接近Ac1=750℃(奧氏體化初始溫度)。但達到一定深度后,溫度超過了HSS(450-600℃)的回火溫度。此外,由于冷卻速率過高,磨削表面出現(xiàn)了高度集中的熱梯度(≈300μm)。
圖8給出了Jaeger分析策略對比,結(jié)果顯示一致性良好;從而證實了數(shù)字模型。圖中的差異主要是由于FE模型的熱對流引起的熱交換所致,而Jaeger模型則沒有考慮該因素。
圖八:不同深度條件下數(shù)值模擬溫度和分析計算溫度
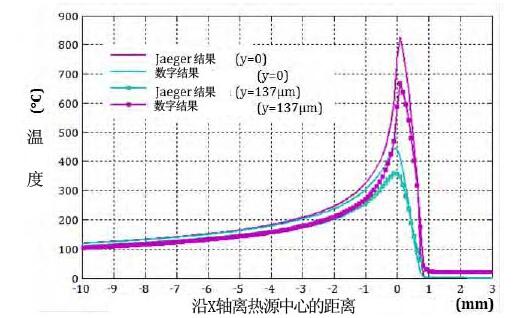
工件速度變化的影響如圖9所示。
圖九:Vw對磨削表面下的溫度輪廓的影響
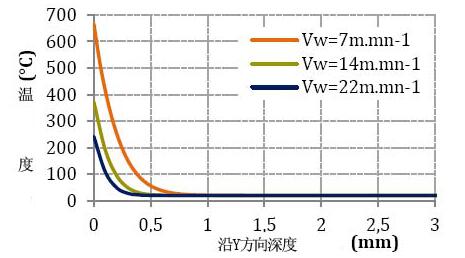
表面溫度和熱影響深度都達到最大,隨工件速度的降低而快速增大。較高的速度縮短了接觸時間從而降低了工件上的熱量。
4.5 預(yù)測殘余應(yīng)力
圖10為沿深度的計算殘余應(yīng)力輪廓(考慮、未考慮砂輪的機械作用),工件速度為Vw=7m.min-1(Tmax=666℃)和Vw=22m.min-1(Tmax=242℃)模擬值和實測值之間的差異是十分顯著的。和實驗測量相比,數(shù)值模擬的結(jié)果表明工件速度對殘余應(yīng)力有非常顯著的影響。在較低速度下,切削和進給兩個方向上都觀察到了較高的表面拉伸殘余應(yīng)力。距離表面100μm距離時,該值逐漸降低至-100MPa(10a)。在較高速度下,磨削表面下觀察到較低的壓縮殘余應(yīng)力。值得注意的是,在所有加工中,砂輪的模擬機械作用對殘余應(yīng)力的分布無影響。
圖十:殘余應(yīng)力輪廓(a)Vw=7m.min-1(b)Vw=22m.min-1
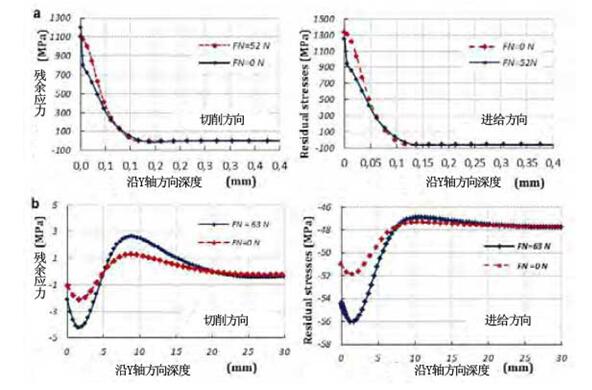
5、討論
實驗結(jié)果和模擬結(jié)果之間的顯著差異說明了高速鋼磨削加工中殘余應(yīng)力來源的很多問題。利用熱機械模型求得的數(shù)字結(jié)果給出了兩種殘余應(yīng)力狀態(tài)類型:當熱效應(yīng)明顯時(Vw=7m.min-1),拉伸殘余應(yīng)力產(chǎn)生,如圖10a;當機械效應(yīng)大于熱效應(yīng)時,產(chǎn)生低壓縮殘余應(yīng)力,如圖10b。本研究所用數(shù)字模型并未考慮相位變換引起的形變和材料回火以及工件上材料的脫落。所有這些現(xiàn)象都會降低拉伸殘余應(yīng)力并提高壓縮殘余應(yīng)力。
由于冶金材料屬性的信息缺失,研究重點主要集中在受影響層面上。磨削加工后,表面試樣被涂附上一層樹脂,然后進行機械
拋光和蝕刻。圖11為改性層面,厚度約5μm。
圖十一:HSS磨削表面微結(jié)構(gòu)的SEM觀察圖
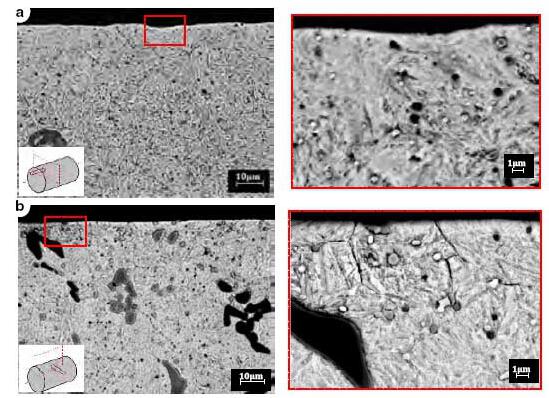
在圖11a中,改性形成的層面可能是由嚴重的塑性變形引起的,也可能是由熱激化奧氏體相變引起。磨削表面的壓縮殘余應(yīng)力也可能是由磨削過程中經(jīng)轉(zhuǎn)化的殘留奧氏體含量所致,如圖11b所示。
此外,臨近磨削表面的EBSD檢測顯示出較低的指數(shù)(黑色區(qū)域),這說明有其他相的存在,其變形的微結(jié)構(gòu)和馬氏體結(jié)構(gòu)是不一樣的。
圖12:HSS磨削表面微結(jié)構(gòu)的EBSD觀察
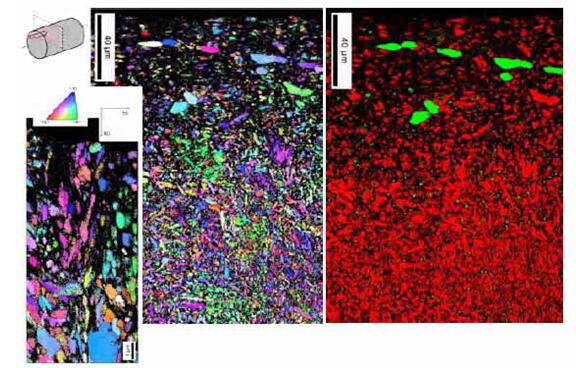
為更多了解改性層的相組份,實驗還進行了磨削前后X射線衍射相分析。結(jié)果顯示磨削和未磨削試樣的馬氏體相的觀察圖是一樣的。
6、結(jié)論
利用CBN砂輪對高合金化高速鋼進行外圓精磨加工后,表面層產(chǎn)生了100μm厚的顯著壓縮殘余應(yīng)力。實驗測量顯示工件速度是外圓磨削過程中最關(guān)鍵的動力參數(shù),它會影響磨削試樣上殘余應(yīng)力的分布。利用熱機械模型求得的熱學(xué)結(jié)果顯示溫度可以大于材料的回火溫度并接近Ac1值。但數(shù)值模擬求得的殘余應(yīng)力和試驗實測值并不匹配。磨削高速鋼微結(jié)構(gòu)的分析說明殘余應(yīng)力是機械、熱學(xué)和變形效應(yīng)共同作用的結(jié)果。變形結(jié)構(gòu)的改性表面層有SEM/EBSD圖可以看出。微結(jié)構(gòu)的變化和磨削過程中殘留的奧氏體相變、回火現(xiàn)象和塑性變形有關(guān)。(編譯:中國超硬材料網(wǎng))