砂帶磨削是一種高效、經濟、用途廣泛,并有“萬能磨削”之稱的新型磨削工藝,它具有“彈性磨削”和“冷態磨削”的特點,因此能獲得很高的加工精度和表面質量[1,2]。 國外將砂帶磨削用于精密、超精密加工,精度已達微米級,表面粗糙度已達到Ra(0.01~0.25)μm[3-6]。我們的實驗表明對細長軸進行開式砂帶磨削能有效地降低表面粗糙度,獲得最優的表面粗糙度可達Ra0.48μm[3,7];本文將以尺寸精度和圓度誤差為研究對象,通過細長軸砂帶磨削實驗,重點研究砂帶磨削后細長軸工件的尺寸精度和圓度的變化,分析影響砂帶磨削加工精度的因素,指出提高砂帶磨削精度的措施。
1 實驗裝置設計及實驗方法
開式砂帶磨削采用成卷的砂帶,通過收帶輪轉動帶動砂帶作緩慢的移動,砂帶由接觸輪壓向工件實現對工件表面的磨削加工。由于砂帶緩慢的移動,磨粒不斷投入磨削,磨削效果一致性好[8]。根據砂帶磨削實驗需要,筆者設計了一臺綜合砂帶磨削裝置,將其裝夾在車床的橫拖板上,并隨車床橫拖板作縱向和橫向進給運動實現砂帶磨削(見圖1)。
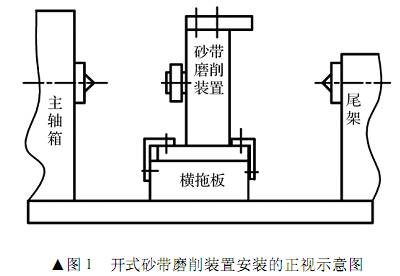
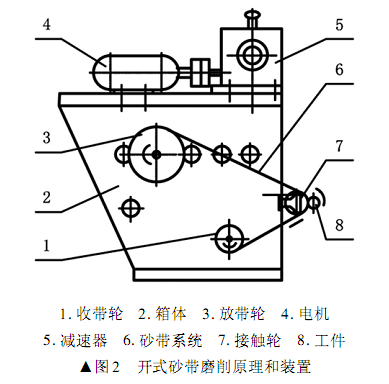
開式砂帶磨削裝置(見圖2)由電機、減速器、放帶輪、收帶輪和接觸輪組成。在該裝置中接觸輪系統是核心結構,其設計制造精度及運動精度會通過砂帶影響加工質量、效率及工作可靠性,為此在設計中接觸輪采用光滑型接觸輪,其外層是一層橡膠,橡膠材料可根據工件精度和表面粗糙度要求不同進行選擇;另外由于接觸輪與工件以直線接觸進行磨削,當接觸輪與工件軸線不平行不僅會導致加工誤差降低砂帶的利用率,同時容易產生砂帶跑偏現象,因此作者將接觸輪系統設計為兩自由度調偏結構(見圖3)。
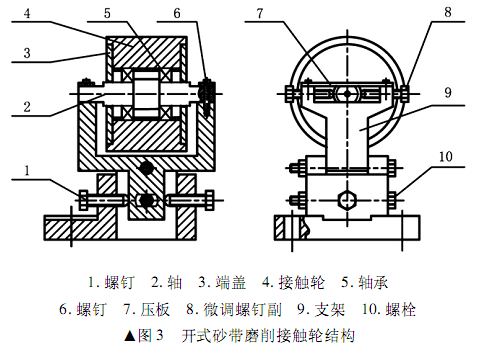
實驗方法:選長徑比為15--20的若干個軸,首先在車床上進行外圓車削,然后用所設計砂帶磨削裝置對工件進行砂帶磨削(干磨)(見圖2),完工后隨機抽取若干工件測量相關數據,分析砂帶磨削前后加工精度的變化。
實驗條件:工件轉速 nw = 1250r/min;砂帶轉速ns = 2r/min;進給量f = 0.01mm/r;平面橡膠接觸輪;工件材料40鋼
2 尺寸精度研究與分析
2.1 實驗數據
隨機抽取四個工件,每個工件在車削完成后,分別在五個截面處從兩個方向測量其直徑尺寸,算出磨削前最大尺寸誤差;之后對工件進行砂帶磨削,磨削完成后,同樣在五個截面處從兩個方向測量其直徑尺寸,算出磨削后的最大尺寸誤差,實驗數據見表1。
實驗數據表明,砂帶磨削前工件尺寸誤差在0.01—0.025 mm,尺寸精度在IT6-IT8范圍內;砂帶磨削后尺寸誤差為0.005-0.017 mm,尺寸精度在IT5-IT7范圍內。可見砂帶磨削后工件的尺寸精度均可提高1-2級以上。同時從實驗數據中可以看出,當車削加工完成后,直接進行砂帶磨削提高尺寸精度是有效的。而且砂帶磨削對工件前道工序產生的錐度、腰鼓肚現象能起到部分消除的作用。

2.2 影響尺寸精度的因素
(1) 微量進給精度。砂帶磨削微量進給精度主要決定于四個因素,一是細長軸剛度弱,磨削時由于磨削力的作用,剛度弱易變形,影響了微量進給精度;二是接觸輪的回轉精度,對于接觸式砂帶磨削將很大程度上影響著微量進給精度;三是接觸輪材料的彈性變形,致使實際切深與理論切深不符,影響微量進給精度;四是車床進給機構、間隙影響微量進給精度。 由于以上四個因素的存在,影響微量進給精度,所以工件尺寸精度的保證受到影響,為此需從上述四個方面采取措施,提高微量進給精度,進而提高工件尺寸精度。
(2) 工藝系統剛度。在加工各部位工藝系統剛度不等的條件下,所加工的工件必然產生相應的軸向形狀誤差,影響尺寸精度。如實驗中對細長軸的磨削,在工件兩端時,工藝系統剛度較高影響較小,但在工件中段工件剛度很低,會產生較大的誤差影響。
(3) 測量誤差。提高測量精度就必須減少測量誤差,以求獲得最真實的結果。因此,一方面合理選擇測量工具或測量方法,另一方面采用多次重復測量,盡可能減少測量誤差。
3 圓度誤差研究與分析
3.1 圓度誤差測量
(1) 測量原理
砂帶磨削后對工件擬采用分度頭測量圓度誤差,用游標原理對線進行讀數。
采用極坐標測量半徑法。利用分度頭將圓周等分為24個測量點。當工件每轉過一個360°/24角時,由千分指示表讀出該點相對某一半徑R的偏差△ri,采用最小二乘圓法評定圓度誤差。即以實際輪廓上各點到某圓周上的距離平方為最小時的圓心為理論圓心,稱最小二乘圓[9,10],最小二乘圓是唯一的,用公式表示為:

式中:εi為被測圓上各點到最小二乘圓之徑向距離
設測量中心為O1,最小二乘圓圓心O(a,b),半徑R,且O1O = e,且令

則:


式中:△ri(i = 1,2,3,……,n)為各測量點測得半徑方向的變化量;
θi(i = 1,2,3,……,n)為各測量點分度的角度值(θi= 360 /24 = 15°) ;
△f0為圓度誤差
(2) 測量數據及結果
隨機抽取5個工件測量圓度誤差,測量時將被測工件頂在分度頭兩頂尖之間,每個工件上分別選擇工件剛度強的截面1和剛度弱的截面5(見表2中圖)各進行一次數據采集。據上述測量原理編寫程序對測量數據進行處理,結果見表2。
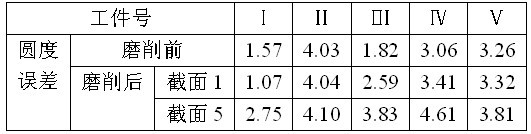
3.2 影響圓度誤差的因素
(1) 主軸回轉精度
通過Taylor圓度儀檢測,工件表面產生棱圓度誤差的主要原因是機床的主軸回轉精度不高引起。因此提高機床主軸回轉精度是降低圓度誤差的主要措施。
(2) 零件定位誤差
在砂帶磨削試驗中,工件以兩端中心孔定位,主軸端采用固定頂尖與雞心卡頭,尾端采用活頂尖。由于活頂尖軸承間隙的影響,降低了頂尖的剛度,產生定位誤差,進而影響圓度誤差[10]。
兩個頂尖和工件上的兩個中心孔本身精度以及它們之間的位置精度對工件回轉精度有重要影響。工件上兩個中心孔本身有形狀誤差時,用其定位對零件外圓進行磨削時,使工件瞬時回轉軸線位置變動,產生橢圓度 工件上兩個中心孔有同軸度誤差時,也同樣會影響零件加工時的回轉精度,產生圓度誤差和直線度誤差,并影響尺寸精度和圓柱度。
(3) 砂帶接觸輪的形狀誤差及回轉精度
對于接觸式砂帶磨削,砂帶與工件呈線性接觸,因此砂帶的支撐體、接觸輪的形狀誤差(圓度誤差和徑向跳動)直接影響被加工工件的圓度誤差。當接觸輪材料較硬時影響較大,較軟時由于材料彈性變形大,對圓度誤差的影響有所減小。從表2的數據可以看出,工件車削后采用砂帶磨削,部分圓度誤差增大,其主要原因就是由于接觸輪形狀誤差和接觸輪偏心所致。
(4) 實驗裝置中電機轉速在600rpm左右,而開式砂帶所需轉速為3-5rpm,因此設計采用渦輪減速器加齒輪減速器進行降速,此裝置裝在機床的溜板箱上,電機和減速器產生的微小振動會傳給砂帶接觸輪,但由于砂帶磨削具有“彈性磨削”的特點,因此振動帶來的影響將大大減小。
4 結 論
實驗表明,在細長軸的加工問題上,當車削完成后直接進行砂帶磨削提高加工精度是有效的。砂帶磨削對工件前道工序產生的錐度、腰鼓度現象能起到部分消除的作用。砂帶磨削后工件的尺寸精度和圓度誤差均可達5-7級以上,較前道工序精度提高1-2級以上。為了更好地提高加工精度砂帶磨削時應注意以下幾點[11,12]。
(1) 優化機床進給機構,提高微量進給精度。普通機床最小微進給在10-20μm,某些數控機床的微進給可控制到5μm,這對利用現有機床進行砂帶磨削提高精度產生一定影響。 因此改進傳統進給系統的結構形式,優化機床進給機構,是提高微量進給精度措施之一。
(2) 提高機床主軸回轉精度、降低圓度誤差。一般情況可用調整軸承間隙和采用高精度軸承來降低主軸徑向跳動和端面跳動,在精密機床中采用液體或氣體靜壓軸承來提高主軸回轉精度。
(3) 確保接觸輪系統的制造精度和裝配精度。當砂帶裝置的接觸輪采用橡膠接觸輪時,由于橡膠材料的彈性變形,致使磨削時的實際切深與理論切深不符,從而影響尺寸精度。因此要獲得良好的尺寸精度,必須合理選用接觸輪材料,采取定量控制接觸輪的變形量,從而提高加工精度。
(4) 提高工藝系統剛度,特別是最薄弱的地方。對細長軸的加工,關鍵是提高工件的剛性,可以采用中心架、跟刀架等工藝措施。
(5) 精加工時,要用合金頂尖研磨工件中心孔,同時保證機床上兩個準確形狀的固定頂尖調整在同一軸線上。
參考文獻
[1] [美]法拉戈 F T.美國磨削技術[M].李長林,譯.北京:機械工業出版社,1991.
[2] 李伯民.實用磨削技術[M].北京: 機械工業出版社,1996.
[3] 李虹.砂帶磨削在普通車床上的應用研究.華北工學院學報,2000,21(1):78~81.
[4] 黃云,黃智.砂帶磨削的發展及關鍵技術[J].中國機械工程,2007,18(9):2263~2266.
[5] 王維朗,潘復生.砂帶磨削技術及材料的研究現狀和發展前景[J].材料導報,2006,20(2):106~108.
[6] 鄧玉平.砂帶磨削在機械加工中的應用[J].水利電力機械,2007,29(11) : 85~86.
[7] 李虹.開式砂帶磨削參數對表面粗糙度影響的分析與優化[J].機械設計與研究,2011, 29(11): 85~86.
[8] 謝國如.基于CA6140 車床砂帶磨削不銹鋼軸的研究[J].金剛石與磨料磨具工程,2004,144( 6) : 65~67.
[9] 李虹,李伯民.圓度誤差測量及誤差分析[J].山西機械,2000,106(1) : 44 ~ 45.
[10] 覃愛梅,黎良新.用分度頭測量圓度誤差的數據處理[J].裝備制造技術,2011,(18) 11: 67-68.
[11] 王啟平.精密加工工藝學[M].北京: 國防工業出版社,1990.
[12] 陳琦,崔瑞明.磨削加工精度分析及提高方法[J].金屬加工(冷加工),2011,32(10):50~52.
作者簡介:李虹( 1966- ) ,女,副教授,主要研究方向:機械設計與制造、精密加工、工程圖學、CAD,發表論文20余篇,省級獲獎1項。
基金項目: 國家自然科學基金資助項目( 51275486)