1. 電解磨削熱噴涂涂層的工藝特點
(1)生產率高
電解磨削可以提高磨削用量,特別是徑向磨削量(磨削深度),可比一般磨削大得多。按單件工時進行統計比較,生產率比一般磨削提高3~5倍。
(2)加工質量好
電解磨削時,砂輪主要是磨除涂層表面上的氧化膜。所以能減輕由于磨削熱、磨削力所引起噴涂層表面的熱應力、殘余應力和變形,加工表面不易產生裂紋和燒傷,尺寸精度與表面粗糙度可達IT7級和Ra 1.25以上。用電解磨削加工噴涂層零件,經使用考核,證明質量合格,效果良好。
(3)砂輪磨耗量小、經濟性好
電解磨削砂輪主要是磨除氧化膜,根據測量,磨削難加工熱噴涂涂層,銅基金剛石導電砂輪,磨除金屬量與砂輪損耗量之比G為400左右(磨削內孔)。
(4)適應性強,加工范圍廣
電解磨削可加工各種難加工導電的熱噴涂涂層,對于各型面(如齒輪表面等)磨削也容易實現。
總之,電解磨削是一種生產率高、加工質量好、經濟實用的加工方法,是加工難加工熱噴涂涂層新的加工方法。
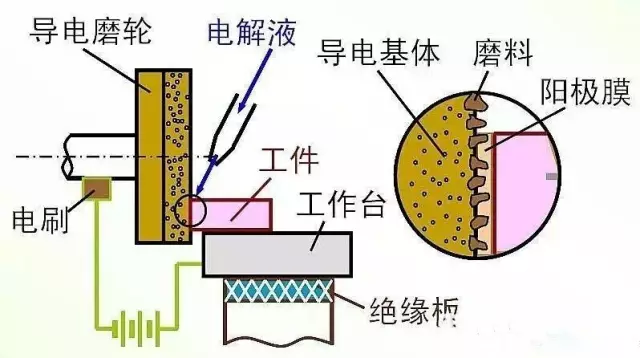
電解液是電解磨削工藝中影響生產率及加工質量極其重要的因素,因為它直接影響陽極電化學反應。根據電化學反應理論,不同成分的電解液,其陽極反應的速度不同,對其反應產物的化學溶解程度也不同。電解磨削過程不但要求氧化,而且也要求鈍化。為了獲得高生產率和良好的表面質量,一般多用亞硝酸鈉或磷酸氫二鈉為主要成分的水溶液(其pH值為8~9)。另外,對電解液的另一個重要要求是不銹蝕機床和危害人體。
電解液的選擇應考慮如下五個方面的要求:
(1)能夠使金屬表面生成結構緊密、粘附力強的鈍化膜,以獲得良好的尺寸精度和表面粗糙度;
(2)導電性能好,以獲得高生產率;
(3)不銹蝕機床與夾具;
(4)對人體無危害,確保人身健康;
(5)經濟效果好、價格便宜、來源豐富,在加工中不易消耗。
要同時滿足上述五個方面的要求是困難的。在實際生產中,應針對不同產品的技術要求、不同材料,選用最佳的應用于電解磨削的電解液。
試驗說明,電解磨削難加工熱噴涂涂層,以磷酸氫二鈉為主要成分的電解液,有較好的磨削性能。
這種電解液的加工效率高,主要是因為除了亞硝酸鈉和硝酸鉀的導電及氧化作用外,磷酸氫二鈉在水溶液中電離后,使溶液呈弱堿性(pH值為8~9),有利于氧化物的溶解,加速了電解過程,從而獲得大的電流效率,使加工效率提高。
通過試驗優選,對于難加工熱噴涂涂層電解磨削的電解液推薦如下:磷酸氫二鈉3%~5%;亞硝酸鈉2%;硝酸鉀2%;水91%~93%。
上述成分的電解液,其pH值為8~9,不銹蝕機床。
3. 電解磨削用設備
電解磨削的機床,可采用專用的電解磨床或普通磨床、車床改裝而成。
電解磨削用的直流電源要求有可調的電壓(5~20V)和較硬的外特性,最大工作電流視加工面積和所需生產率可自10~1000A不等。只要功率許可,一般可以和電解加工的直流電源設備通用。
供應電解液的循環泵一般采用小型離心泵,但最好是耐酸、耐腐蝕性的,還應有過濾和沉淀電解液雜質的裝置。在電解過程中有時會發生對人體有害的氣體,如一氧化碳等。因此在機床上最好設有強制抽氣裝置或中和裝置,至少應在空氣較流通的地點操作。
電解液的噴射一般都用管子和扁噴嘴,噴嘴接在管子上,向工作區域噴注電解液。內圓磨頭由高速砂輪軸與三相交流電機組成。高速砂輪軸的徑向擺差≤0.01 mm,轉速5000~6000 r/min。三相交流電機功率0.75 kW,轉速2800 r/min。它安裝在車床的溜板上,并與溜板絕緣。砂輪軸心線與車床主軸中心同高。車床主軸的改裝主要是使卡盤與主軸絕緣,并在主軸末端裝上陽極電刷,它與直流電源箱的輸出正極相接。
直流電源可采用硅整流直流電源,輸出電壓0~30V,輸出電流0~200A。能無級調壓,并有過壓、過電流保護裝置。
電解液泵可采用機床冷卻泵,電解液可由機床的冷卻液箱經膠皮管通過主軸孔直接噴在零件上,再由回液管流回電解液箱。
4. 電解磨削的工藝參數
(1)砂輪的工藝參數
砂輪可采用金剛石青銅粘合劑的導電砂輪,也可采用石墨、滲銀導電砂輪。砂輪速度υ=15~20 m/s;軸向進給量?a=0.5~l.0 m/min(內外圓磨);?a=10~15 m/min(平面磨);工件速度υw=10~20 m/min;徑向進給量?r =0.05~0.15 mm/dst。
(2)電壓、電流規范
根據以上電解液的試驗所得的電流效率特性曲線,可得最佳電流密度與電壓。粗加工電壓8~12V;電流密度20~30 A/cm2;精加工電壓6~8V;電流密度l0~15 A/cm2。以上工藝參數在應用時,如磨削表面出現燒黑現象,應降低電壓或減小徑向進給量,增大軸向進給量。