引言
機(jī)械合金化(MA)作為一種粉末加工工藝,粉末顆粒要經(jīng)過(guò)反復(fù)的形變、碎裂和鍛接。MA廣泛應(yīng)用于材料合成:類似金屬間化合物,過(guò)飽和固溶體,或者穩(wěn)定/不穩(wěn)定硼化物、碳化物、氮化物和硅化物的成形。鋁合金中摻入陶瓷硬質(zhì)顆粒通常是為了增加強(qiáng)度,顯微硬度和耐磨性。但選擇一個(gè)研磨優(yōu)化參數(shù)對(duì)于工件的機(jī)械性能也很重要,本研究中的燒結(jié)時(shí)間、燒結(jié)溫度和成型壓力等都視為重要的研磨參數(shù)。另外,碳化硅顆粒增強(qiáng)的不均勻分布或結(jié)塊都能導(dǎo)致材料的強(qiáng)度、延展性和韌性的降低。因此,研磨參數(shù)的優(yōu)化就可以改善材料的機(jī)械性能。碳化硅顆粒增強(qiáng)鋁基復(fù)合材料由于較高的強(qiáng)重比、良好的耐磨性和韌性以及抗疲勞性而廣泛應(yīng)用于航空和汽車制造行業(yè)。
實(shí)驗(yàn)材料和實(shí)驗(yàn)步驟
實(shí)驗(yàn)用10 vol% 的碳化硅(20μm)對(duì)工業(yè)級(jí)鋁粉進(jìn)行增強(qiáng)處理,用SEM、XRD和EDX觀察鋁粉和碳化硅的尺寸、形狀和化學(xué)組份,如圖一,圖二所示:
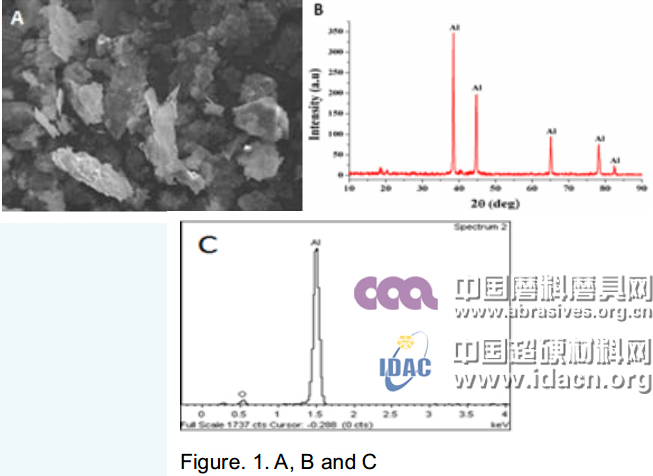

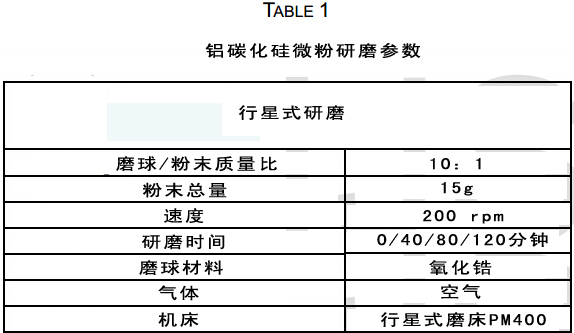
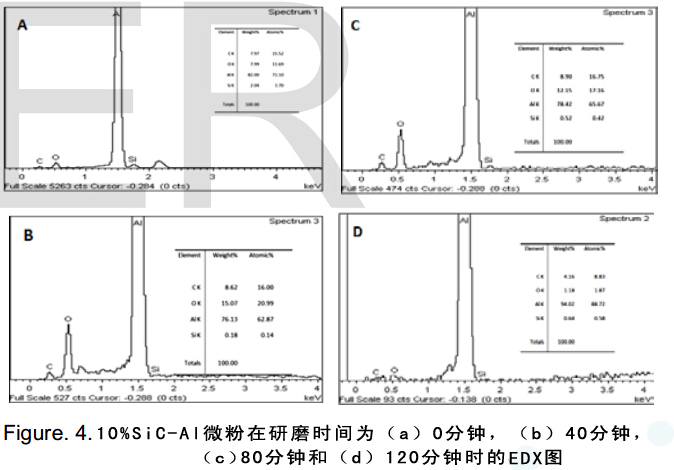

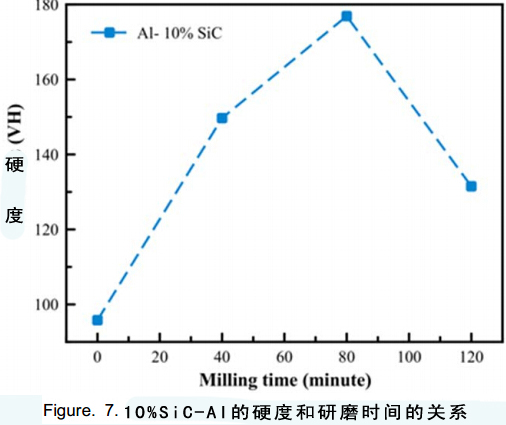
實(shí)驗(yàn)結(jié)果和討論
粉體形狀
研磨時(shí)間分別在0、40、80和120分鐘時(shí)將碳化硅混入鋁粉。碳化硅份量為10%,其余為鋁粉。實(shí)驗(yàn)過(guò)程中,研磨時(shí)間對(duì)顆粒尺寸和顆粒分布的影響很明顯:用SEM觀察研磨時(shí)間分別為40,80分鐘時(shí)顆粒尺寸變?。坏?20分鐘時(shí)由于加工硬化而出現(xiàn)顆粒尺寸變大現(xiàn)象,這主要是由于碳化硅分布不均勻并結(jié)塊而致,如圖三(A和B)所示:
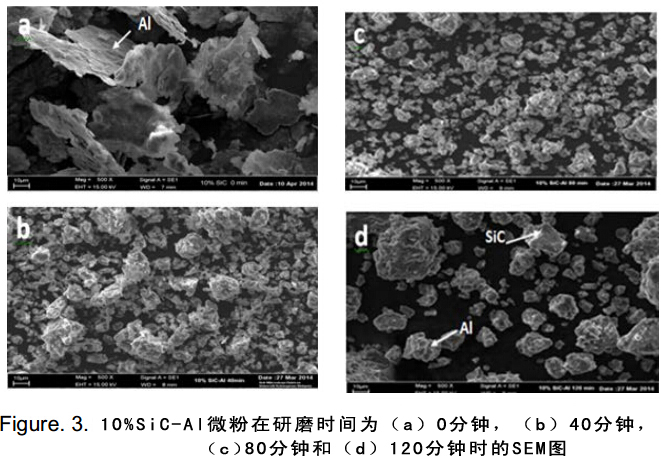
圖六為10% SiC-Al復(fù)合材料的光學(xué)顯微像。研磨時(shí)間為0分鐘時(shí),碳化硅在鋁基中分布不均,但顆粒結(jié)構(gòu)清晰可見(jiàn)。隨著研磨時(shí)間增至40分鐘和80分鐘時(shí),顆粒結(jié)構(gòu)逐漸消失。試樣中可以觀察到SiC周圍的多孔性。研磨時(shí)間為120分鐘時(shí),復(fù)合材料由于基體的嚴(yán)重形變而開(kāi)始發(fā)生離析。
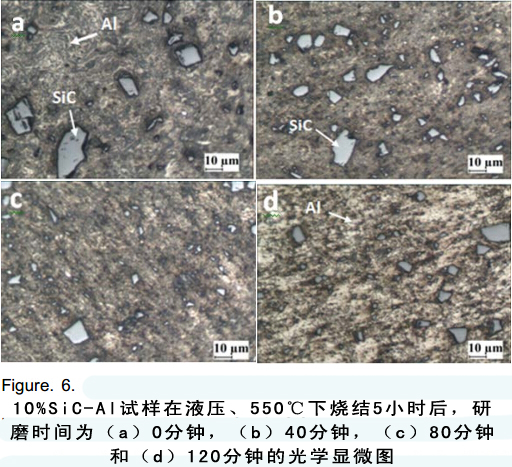
硬度測(cè)試
實(shí)驗(yàn)對(duì)碳化硅鋁復(fù)合材料(直徑12.7mm,高度4.5mm)式樣施加10kg的負(fù)荷。硬度隨研磨時(shí)間增長(zhǎng)而變大,研磨時(shí)間為80分鐘時(shí),由于基體發(fā)生形變,硬度達(dá)到最大值。在該階段鋁基體形變可能會(huì)產(chǎn)生晶格畸變并引起晶格應(yīng)變,從而加劇錯(cuò)位,也即硬度機(jī)理。研磨時(shí)間達(dá)到120分鐘時(shí),由于基體的粒徑拉伸而引起離析,錯(cuò)位不再是主要影響因素。
抗壓測(cè)試
實(shí)驗(yàn)用液壓機(jī)制造出直徑1.5mm高度10mm的試樣,550℃下燒結(jié)5小時(shí)。
圖八(a)為研磨時(shí)間0分鐘時(shí)的最大抗壓144Mpa;抗壓強(qiáng)度隨研磨時(shí)間增大而增大。(b)為研磨時(shí)間40分鐘時(shí)抗壓強(qiáng)度增至212Mpa;(c)為80分鐘時(shí)抗壓強(qiáng)度增至270 Mpa;(d)為120分鐘時(shí)抗壓強(qiáng)度降至221 Mpa,這是由于加工硬度及上升溫度引起離析的緣故。
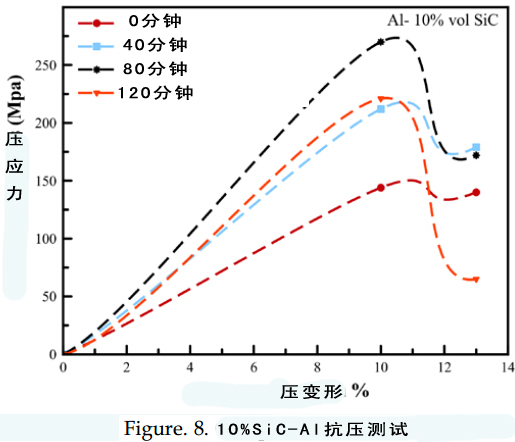
結(jié)論
隨著研磨時(shí)間分別增至0、40、80和120分鐘,碳化硅鋁微粉的形狀由剛開(kāi)始的薄片逐漸被破碎,只有在120分鐘時(shí)由于加工硬化而出現(xiàn)顆粒尺寸變大現(xiàn)象。
隨著增強(qiáng)顆粒的增多,冷焊和破裂機(jī)制更加顯著并出現(xiàn)了均勻結(jié)構(gòu)。壓力應(yīng)變曲線圖證明隨著研磨時(shí)間的增大、增強(qiáng)顆粒尺寸和數(shù)量的增多以及初始密度的增大,試樣的延展性降低而硬度變大。硬度和抗壓應(yīng)力隨著研磨時(shí)間增長(zhǎng)而變大,但在80分鐘之后由于磨粒形變引起鋁碳化硅之間的離析而開(kāi)始降低。
(翻譯:中國(guó)磨料磨具網(wǎng))