摘要 對電鍍金剛石線鋸鋸切微晶玻璃的工藝參數進行了試驗優化研究。設計了3因素4水平的正交試驗,分析了工件進給速度、鋸絲線速度和氣缸壓力對切片表面粗糙度和鋸切效率的影響,獲得了基于降低表面粗糙度和提高鋸切效率的鋸切工藝參數。在本試驗范圍內,優化的工藝參數為:工件進給速度0.75mm/min、鋸切線速度1.7m/s,氣缸壓強0.26MPa。
自從微晶玻璃出現以后,在短短的二三十年時間里,就廣泛應用于電子、化工、生物醫學、機械工程、軍事和建筑等領域。微晶玻璃的加工越來越受到重視,由于微晶玻璃硬度高、韌性小、導熱性差,加工點附近的溫度容易上升,刀具的磨損較大,這決定了切割微晶玻璃的刀具不同于金屬加工,不能采用硬質合金或高速鋼或其他金屬加工用的刀具,微晶玻璃一般采用金剛石刀具進行機械加工,這樣就可以避免玻璃開裂或崩角等現象,還可以提高加工效率。
固結磨料金剛石線鋸[1-2]是指通過采用某種技術或工藝方法將高硬度、高耐磨性的金剛石磨粒牢固地固結在鋼絲基體表面上而制成的一種切割工具[3],非常適合加工微晶玻璃。固結磨料金剛石線鋸具有切縫窄、鋸切效率高、切片質量好、對環境污染小、能加工大直徑工件和超硬材料等優點[4],在硬脆材料的加工方面得到了較為廣泛的應用[5]。綜上所述,固結磨料金剛石線鋸是目前比較適合微晶玻璃等脆硬材料的切割工具。我們采用電鍍金剛石線鋸切割微晶玻璃,研究鋸絲線速度、材料進給速度、鋸絲張力與表面粗糙度和鋸切效率的關系,分析影響切割表面質量的因素,為提高表面質量和鋸切效率確定最優化的工藝參數。
1 試驗原理與設備
采用XD-170型金剛石線旋轉點切割機,實物如圖1所示。鋸絲運動方式為往復式,X,Y軸移動平臺由雙直線導軌支撐,精密絲杠/步進電機驅動,單片機控制,進給速度可無級調節,在0.025~18mm/min之間可精確控制切割厚度。X軸移動平臺上裝有十安夾具,可實現對棒料的夾持。本次試驗使用的是橫截面為正方形的棒料,切割阻力不隨切割深度變化而變化,使切割面面形一致,從而實現被切材料的平整度、平行度能夠達到所需的技術指標。
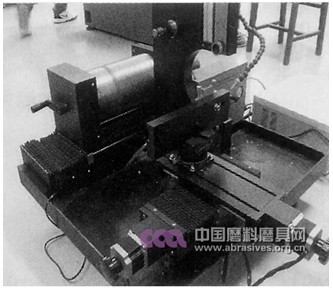
使用電鍍金剛石鋸絲切割微晶玻璃,鋸絲直徑為0.5mm,電鍍金剛石顆粒的平均直徑為30~40μm,工件進給速度范圍為0.25~0.75mm/min,鋸絲線速度為1.5~1.8m/s,氣缸壓強為0.2~0.26MPa。切割材料為鋰鋁硅系微晶玻璃,該系列玻璃具有良好的耐熱性和零膨脹的特性,硬度高,但是韌性小。
實驗采用德國MAHR公司生產的S3P表面粗糙度測量儀,如圖2所示。能測量下列三個參數任意一個:Ra,Rmax,Rz,且可選擇相互替換。可以在水平,垂直或倒置位置上進行測量,其測量范圍為Ra0.02~25μm。
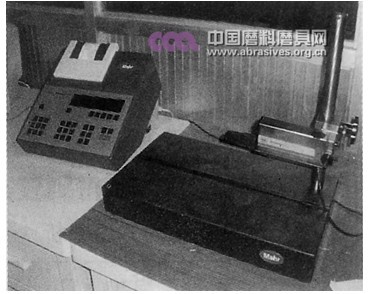
2 正交試驗設計及結果
影響切片質量和鋸絲壽命的鋸切工藝參數有鋸絲線速度、鋸絲張緊力和工件進給速度等因素。為了提高鋸切效率和切片質量,有必要對鋸切工藝參數優化,為此,設計了一組正交試驗。試驗時,改變張緊支持輪的氣缸壓力,從而改變鋸絲上的張緊力。通過控制箱上的調速裝置來控制電機轉速,可得到不同的鋸切速度(即鋸絲線速度)。由X軸移動平臺的調速器來控制工件的進給速度。
影響因素:鋸切速度、鋸絲張緊力和工件進給速度,每個因素取四個水平,因素水平表見表1。粗糙度測量方法采用垂直切削紋路,沿進給方向依次測量三次取平均值的方法,確定微晶玻璃切片最終的粗糙度值。鋸切工藝參數優化正交試驗計劃及試驗結果見表2。
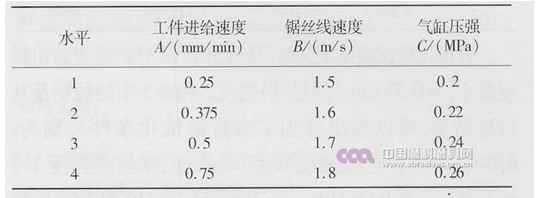
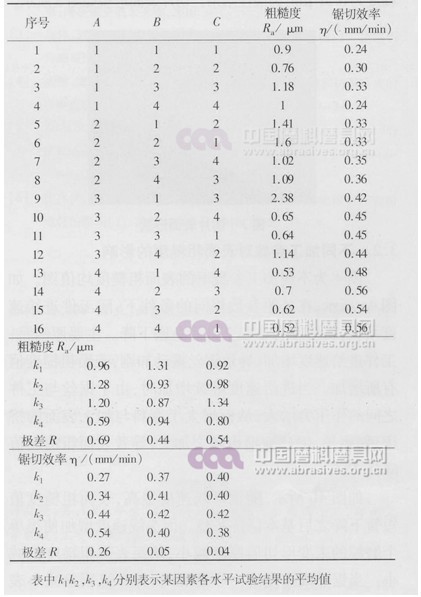
3 試驗結果分析
3.1 表面粗糙度正交試驗分析
對表面粗糙度的方差分析結果見表3。可見,工件進給速度對切片表面粗糙度值的影響最大。各加工參數對切片表面粗糙度的影響主次順序依次為:工件進給速度,鋸絲線速度,氣缸壓強。
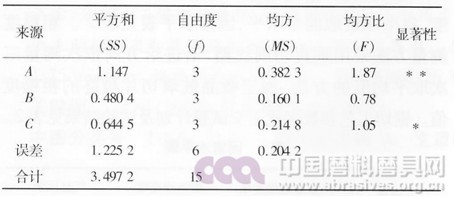
直接比較試驗結果,很容易看出第13號試驗表面粗糙度最小,為0.53μm。但是,根據表2和表3中的數據及其計算結果,可以得出各加工參數的優化條件分別為:A4B3C4即工件進給速度0.75mm/min、鋸絲線速度1.7m/s,氣缸壓強0.26Mpa。經試驗驗證,此時的切片表面粗糙度為0.51μm,為最佳結果。切片表面形貌如圖3所示。

3.2 不同加工參數對表面粗糙度的影響
圖4為不同加工參數下的表面粗糙度均值圖。如圖4a所示,在其他參數相同的條件下,隨工件進給速度增大,粗糙度有小幅上升后急劇下降。主要原因是:工件進給速度增加,導致鋸絲振動加劇,表面粗糙度值有所增加。當進給速度繼續增加時,由于鋸絲與工件之間的作用力增大,從而增大了磨料與加工表面的擠壓、劃擦等,鋸絲變形也隨之加大,導致表面粗糙度值降低[6]。
如圖4b所示,隨鋸切絲速度提高,表面粗糙度值短暫下降之后基本保持平穩。因為線速度增加使得單個磨粒的未變形切屑厚度減小,從而表面粗糙度值減小。當鋸絲線速度進一步增加時,并不能明顯減小表面粗糙度值,其原因主要是,線速度增大,使得鋸絲與工件之間的沖擊力增大,系統振動加劇,從而破壞了鋸絲相對工件的正確位置[6]。
如圖4c所示,氣缸壓強值的大小主要反映了鋸絲的張緊力的大小。張緊力越大,鋸絲的振動頻率隨之增大,導致切片表面的紋路增加,表面粗糙度值上升。但是當張緊力達到一度閾值,振動會減小,切片粗糙度會得到改善。

3.3 鋸切效率的試驗分析
由表4鋸切效率的方差分析可以看出:工件進給速度對鋸切效率的影響最大。其他加工參數對鋸切效率的影響很小,可忽略不計。所以只要保證進給速度在工藝允許的范圍內最大,就可以得到較高的鋸切效率。從提高表面粗糙度和鋸切效率的角度考慮,提高工件進給速度是最有效的方法。可以直接選取上述優化條件A4B3C4。
圖5為不同工藝參數下鋸切效率的均值圖。如圖5所示,隨工件進給速度增加,鋸切效率增加。鋸絲線速度和氣缸壓強對鋸切效率幾乎沒有影響,與試驗分析結果一致。原因在于:平均單顆磨粒的去除量是不變的,當工件進給速度增加時,總的去除量是增加的。而鋸絲線速度和氣缸壓強增加時并不能增加總的去除量,所以鋸切效率主要受工件進給速度影響。
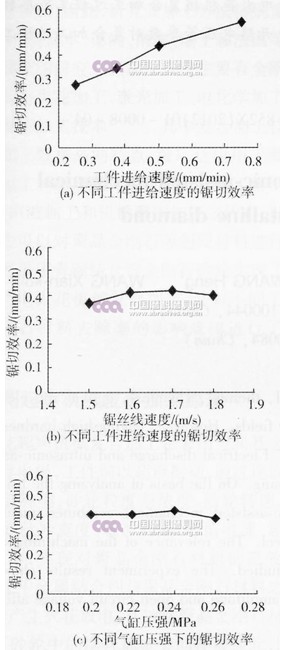
4 結論
在電鍍金剛石線鋸切割機床上,對微晶玻璃進行了鋸切試驗,用正交試驗方法對鋸切工藝參數進行了優化。結論如下:
(1) 工作進給速度對表面粗糙度和鋸切效率影響最大,提高工件進給速度有助于降低表面粗糙度值,提高鋸切效率。
(2) 鋸絲線速度和氣缸壓強對于鋸切效率幾乎沒有影響。
(3) 鋸切微晶玻璃時,為保證較高的鋸切效率和最佳表面粗糙度,在本試驗范圍內,最佳工藝參數為:工件進給速度0.75mm/min、鋸絲線速度1.7m/s,氣缸壓強0.26Mpa.
參考文獻:
[1] 孟劍峰,孟磊,韓云鵬。環形金剛石線鋸加工參數優化[J]。金剛石與磨料磨具工程,2008(5):35-38.
[2] 趙禮剛.金剛石線鋸切割半導體陶瓷的機理與工藝研究[D].南京:南京航空航天大學,2010.
[3] 高偉,劉迎.環形電鍍金剛石線鋸鋸切工藝參數優化[J].金剛石與磨料磨具工程,2005(6):54-55.
[4] 高偉,竇百香,劉偉.固結磨料金剛石線鋸制造方法和切割形式的研究進展[J].金剛石與磨料磨具工程,2008(5):30-34.
[5]ZHAO L G,ZUO D W,SUN Y L,et al.The analysis on the Stability of Diamind Wire Saw Cutting Process of the Silicon[J].Key Engineeting Material,2009,407-408:684-689.
[6] 沈兆俠,陳榮發,孫玉利,等.金剛石線鋸切割對砷化鎵切片表面質量的影響[J].揚州大學學報,2010,13(2):33-36.
作者簡介
楊楊,男,1986年生,南京航空航天大學碩士研究生,研究方向:精密加工。