摘要 作者:李印江教授§1概述有機磨具是在1880年出現,當時用天然的蟲膠做結合劑,以后有了人造樹脂,有機磨具才迅速發展起來。到了1980年在世界范圍內樹脂磨具與陶瓷磨具的產量比已超過1...
作者:李印江 教授
§1 概述
有機磨具是在1880年出現,當時用天然的蟲膠做結合劑,以后有了人造樹脂,有機磨具才迅速發展起來。到了1980年在世界范圍內樹脂磨具與陶瓷磨具的產量比已超過1 :1,現在仍有增長的趨勢。樹脂磨具所以能迅速的發展,主要有以下幾方面的特點:
1、結合強度高,如高速切割砂輪使用線速度可達80-100m/s,重負荷砂輪磨削負荷由過去的50kg左右提高到1000kg以上。
2、便于調整結構和性能,樹脂磨具的硬化溫度只有200℃左右,比陶瓷磨具1300℃的燒成溫度低的多,因此可以在磨具鋃入網格布、金屬絲、石墨粉、螺帽等材料,以適應不同磨削的需要。許多填料的性能在制成磨具后仍能保持,所以使用不同的填料能在很大放范圍內改變磨具的性能。
3、樹脂磨具有一定的彈性,有利于提高被加工工件的光潔度,選用石墨、氧化鉻等拋光材料作填料還可以進一步降低粗糙度。
4、加工中不易燒傷工件, 樹脂在230℃上就逐漸炭化,加工中的高溫使樹脂局部炭化,產生自銳,提高了磨削的鋒利度從而又降低了磨削溫度,避免燒傷工件。
5、由于樹脂具有良好的成型性能,又有很好的韌性,所與可以制成約0.1mm厚度的薄片砂輪,用于開槽切割。
6、樹脂磨具生產周期短,設備簡單,投資少見效快。是許多磨具廠的起步產品。
7、樹脂磨具耐水性差、耐堿性差, 保存期短,是其缺點,生產和使用中應予以注意。
8、樹脂磨具大量用于制造切斷砂輪、鈸形砂輪、重負荷砂輪、軋輥拋光砂輪、石墨鏡面磨砂輪、導電磨砂輪、珩磨輪、柔軟拋光砂輪等。
§2 樹脂磨具的結構和性能
一、樹脂磨具的結構
通常所說的磨具三要素五因子主要是以陶瓷磨具為對象而論,對樹脂磨具應是四要素六因子, 四要素是磨料、結合劑、填充鋃嵌材料和氣孔。
(1)磨料 作為切削刃,切削工具,是磨具的主要組成部分。
(2)結合劑 起著粘結磨粒和各種填充和鋃入材料的作用,使磨具得以成型。
(3)填充鋃嵌材料 賦予磨具各種獨特的性能如導電性、拋光性和使用磨具帶有中孔以外的安裝結構等,如螺栓緊固砂輪。
(4)氣孔 是指磨具內部具有的孔隙,有助于冷卻和排屑作用。
二、樹脂磨具的性能
樹脂磨具的性能由樹脂磨具的六因子確定,六因子是:磨料材質、磨料粒度、結合劑(樹脂)性能、磨具硬度、磨具組織和填充材料性能。
(1)磨料材質 磨料有多種如棕剛玉、白剛玉、黑碳化硅、綠碳化硅等,不同的磨料有不同的性能,適用不同磨削對象的需要,也決定了磨具的性能。
(2)磨料粒度 相同的磨料不同的粒度的磨具,對被加工工件的精度, 粗糙度,加工效率等方面都有明顯的影響。
(3)結合劑 各種樹脂的粘結強度、耐熱性、耐磨性和穩定性均有不同,所以用不同的樹脂作結合劑時磨具的性能也不同。
(4)硬度 不同加工質量和不同材質的工件對磨具的硬度有不同的要求,同時硬度對加工效率也有很大的影響。
(5)磨具的組織 磨具的組織用磨粒在磨具中所占的體積百分數來表示,磨粒占的體積百分數大則磨具中的氣孔少,磨粒占的體積百分數小氣孔多,所以磨具的組織間接的反映磨具的氣孔的多少,但它并不等同的對應于氣孔率的大小,這是應該注意的。
(6)填料 由于樹脂磨具的硬化溫度低,所以磨具制成后混料時加入的某些填料仍然保持著原有的特性,如銅粉、石墨粉的導電性,某些填料的拋光性能和高分解性能等都影響著磨具的特性,所以對于樹脂磨具這第六個因子是不能少的。
(7)除以上決定磨具性能的六因子以外,在制造過程過所產生的一些性能,如平衡性和幾何精度等也對磨具質量有很大影響。
§3 樹脂結合劑磨具常用的樹脂
作為結合劑用樹脂的要求:
(1)對磨料有很強的結合能力。
(2)有較高的耐熱性能。
(3)有很高的抗拉、抗壓、抗沖擊強度。
(4)具有良好的制造和加工性能。
具有這些特點的常用樹脂有:酚醛樹脂、環氧樹脂、新酚醛樹脂、聚胺基雙馬來酰亞胺樹脂、聚乙烯醇縮醛等。
一、酚醛樹脂
酚醛樹脂是由苯酚和甲醛在酸、堿觸媒作用下合成的。由于工藝不同可以制成液體酚醛樹脂和粉狀酚醛樹脂兩種。
1、制造酚醛樹脂的原材料
(1)苯酚
苯酚又稱石炭酸,純白無色針狀晶體,在空氣中可氧化成淺粉色。
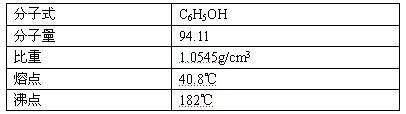
苯酚能溶于熱水,溶于酒精,堿等。有弱酸性,易滲入皮膚,引起過敏現象。將2%左右的苯酚肥皂水溶液用于消毒,醫用名稱“來蘇兒”。
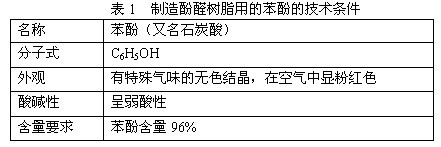
(2)甲醛
甲醛為無色氣體,用于制造酚醛樹脂的是甲醛的水溶液。
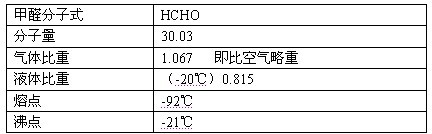
甲醛溶于水和酒精,40%的水溶液醫學上稱 “福爾馬林”,做防腐劑使用。長期存放的甲醛易聚合沉淀出白色塊狀物,加入8-12%的甲醇(CH3OH)可防聚合。甲醛具有強烈的刺激性氣味,能刺激眼睛和呼吸道粘膜,并引起皮膚過敏現象。甲醛的技術條件見表2
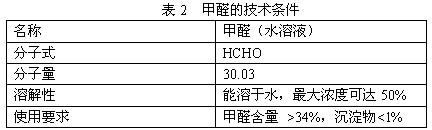
(3)催化劑
① 堿性催化劑 氫氧化鈉、氫氧化鋇、氫氧化銨等都可以做合成酚醛樹脂的催化劑生成液體酚醛樹脂。
磨料磨具行業用的液體酚醛樹脂通常是用氫氧化銨作催化劑,因氫氧化銨屬于弱堿性。對不耐堿地酚醛樹脂影響不大。殘留部分在硬化加熱時大部分揮發掉了,所以用氫氧化銨作催化劑的酚醛樹脂具有較高的強度,耐水性較好。氫氧化鋇也是較好的催化劑;而氫氧化鈉是一種強堿,殘留在磨具的結合劑中對磨具有破壞作用,因此在磨具制造中很少使用氫氧化鈉作催化劑的酚醛樹脂。
苯酚與甲醛生成樹脂的反應速度隨催化劑的用量增多而加快,但是反應太快則不易控制,通常氫氧化銨的水溶液用量為苯酚的3-6%。
作為催化劑的氫氧化銨含量不小于17%,比重為0.88-0.92 g/cm3。
②酸性催化劑 生產粉狀的酚醛樹脂通常使用鹽酸作催化劑。鹽酸是氯化氫的水溶液。工業鹽酸的氯化氫含量為25-40%,比重為1.12-1.20。用量以苯酚為100%計,鹽酸加入量,以純HCl計為0.1-0.3%。殘留在樹脂中的鹽酸在硬化加熱過程中幾乎全部揮發掉,對樹脂性能沒有明顯影響。
2、液體酚醛樹脂的生產工藝
(1)生產液體酚醛樹脂時甲醛的加入量要比正常的需要量略多一些,甲醛量多一些樹脂的生產速度快,產量高,游離酚減少。通常取苯酚與甲醛的克分子比為:6 :7;催化劑氨水加入量為苯酚加入量的4%,(氨水中氫氧化銨含量按25%計時)。當混合物料加熱到85℃左右時,可停止加熱,物料以縮聚反應放出的熱量自行升溫到98℃左右,并開始沸騰,當反應過于激烈時應通水冷卻。
(2)液體酚醛樹脂的生產工藝流程,見圖1
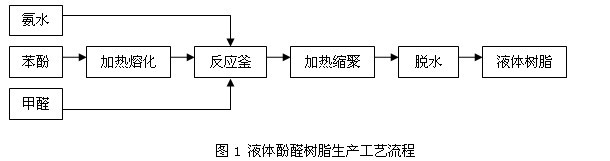
樹脂合成后采用真空脫水,水分和揮發分脫除的比較干凈,過多的水分和揮發分殘留在樹脂中在磨具硬化時易發泡。酚醛樹脂生產設備示意圖見圖2。
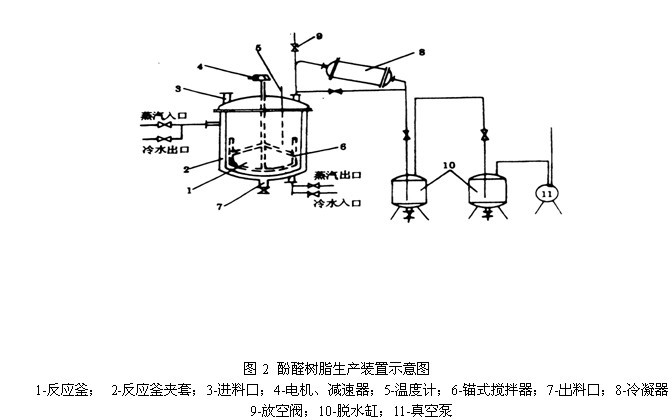
(3)液體酚醛樹脂的性質 液體酚醛樹脂常溫下是棕紅色粘稠液體,有刺激性氣味。比重1.15-1.2。能溶于乙醇、丙酮、糠醛等溶劑中。樹脂中游離酚含量為10-18%。
液體酚醛樹脂在100℃的溫度下保持2個小時仍有流動性,屬甲階,稱A型,A型的特點是能溶于酒精中。
在120℃保持2小時則失去流動性,變為乙階、稱B型。B型樹脂的特點是不溶于酒精,但略有膨脹,成彈性體。在130℃以上保持2個小時則成堅硬的固體,屬丙階,稱C型。C型樹脂的特點是不溶于酒精,不變形;加熱不溶化;加熱到230℃以上則炭化。
(4)液體酚醛樹脂的性質對磨具性能的影響
① 樹脂粘度 液體樹脂的粘度和溫度和固體含量有關,固體含量高、溫度低則粘度高,反之則粘度低。作為粉狀酚醛樹脂潤濕劑使用時,低粘度的溶解能力較強,生產的磨具機械強度較高;樹脂的粘度用落球法或杯流法測定。作為粉狀潤濕劑使用的液體酚醛樹脂的粘度一般用杯流法測定,數值在40-400秒之間。
② 游離酚的影響 液體酚醛樹脂中有一部分沒有參加反應的苯酚,稱為游離酚。游離酚在做為潤濕劑的樹脂中應控制在28%以下。雖然游離酚的這個數值較高,但因為苯酚可以溶解粉狀樹脂,使型料有較好的可塑性,有利于樹脂對磨粒的粘結,可以提高磨具的強度。
③ 固體含量 將重量為W1(約5-10克)的樹脂在150℃-180℃的溫度下加熱1小時的剩余量W2,按式(1),(2)計算出x稱固含量,y為聚合損耗。

x ——固體含量
y ——聚合損耗
W1——加熱前樹脂量
W2——加熱后樹脂量
對于用粉狀樹脂生產磨具,作為潤濕劑的液體酚醛樹脂只占樹脂總量的1/3左右,而且也可以和粉狀樹脂的數量互換,因液體量大時對磨料潤濕好,對粉狀樹脂的溶解增強,所以雖然液體樹脂的固體含量較低,但液體酚醛樹脂用量增加并不降低磨具的強度和硬度。作為潤濕劑的酚醛樹脂其固體含量要求大于65%,聚合損耗小于35%。
3、粉狀酚醛樹脂的生產工藝
(1)粉狀酚醛樹脂生產中苯酚與甲醛的比例與液體樹脂生產中甲醛過量相反而是苯酚過量,苯酚與甲醛的克分子比為7 :6 ,催化劑使用鹽酸,約0.2%左右,其工藝流程與生產液體酚醛樹脂大致相同。產品冷卻后成淡黃色半透明固體塊狀,經粉碎過篩后成粉狀。
(2)粉狀酚醛樹脂是熱塑性樹脂,制造磨具時需要加入硬化劑使之轉變成熱固性的樹脂。常用的硬化劑是烏洛托品,亦稱六次甲基四胺。烏洛托品由甲醛和氨制成,為白色結晶粉末,比重為1.27(25℃),溶于水和酒精。分子式(CH2)6N4。加入量為樹脂的6-10%。可以在樹脂粉碎時加入,也可以在使用前加入。烏洛托品加入量太少不足以使樹脂硬化,加入量太大增加揮發物排出量,也會降低磨具的強度和硬度。以8%左右為宜。
(3)粉狀樹脂的軟化點,軟化點實際上反映了樹脂的的聚合程度,聚合程度高則軟化點高,反之亦然。軟化點低的樹脂粉碎時發粘,放置時易結塊。混合的型料也易結塊。軟化點過高雖然型料比較松散。但是成型壓合性差,也影響磨具強度。一般要求粉狀樹脂軟化點在85-115℃之間,以90-105℃為宜。但是隨冬夏季節氣溫的變化應將軟化點略加調整,氣溫低時軟化點也低些,氣溫高時軟化點也高些。
(4)粉狀酚醛樹脂的游離酚含量通常在5.5%左右。
(5)粉狀酚醛樹脂的粒度 粉狀酚醛樹脂要與硬化劑混合,過粗的程度不利于相互接觸,所以粉狀樹脂的粒度組成要求240#以細的粒度大于80%,100#篩余小于3%。
二、環氧樹脂
環氧樹脂是環氧氯丙烷與二酚基丙烷以氫氧化鈉做催化劑加熱縮聚而成。
1、環氧樹脂的性質
(1)環氧樹脂有液體和固體兩種,均為淡黃色,屬熱塑性,性質穩定,可長期儲存,易溶于丙酮、甲苯等溶劑。在固化劑作用下可加熱硬化,而呈熱固性。
(2)具有較強的粘結力 環氧樹脂有極為活潑的環氧基,能生成化學鍵與接觸面反應聯結,另有羥基和醚基與接觸表面產生電磁引力,所以有很強的粘結能力。
(3)固化時收縮小,尺寸穩定性能好,熱膨脹系數小,生產中不易出現裂紋等廢品。
(4)耐化學浸蝕性好,耐堿,耐酸也耐有機溶劑。
(5)環氧樹脂的最大缺點是耐熱性能差,其耐熱性能隨固化劑不同而有很大變化,但不論那種固化劑他的耐熱性都較酚醛樹脂差的多。
2、環氧樹脂的特點
(1)具有較高的強度和硬度,相同條件下的回轉線速度,酚醛結合劑為108m/s,環氧樹脂結合劑為126m/s以上。
(2)因其耐熱性差,使用中磨損大,消耗高;但因其耐熱性差而自銳性好,不易燒傷工件,在某些方面的應用也是他的優點。
(3)環氧樹脂的固化劑,環氧樹脂可加入固化劑加熱硬化,固化劑參加化學反應,成為樹脂的組成部分,硬化后成為不溶不熔的固體物質。
① 胺類固化劑 主要是乙二胺、三乙醇胺,間苯二胺等。胺類固化劑可以“冷硬化”,即在不加熱的情況下固化,固化迅速。但其耐熱性較低,通常用于澆注珩磨輪。如果制品在100℃以下加熱一段時間,則固化的更好。
② 酸酐類固化劑 酸酐類固化劑需要加熱固化,固化溫度在130℃以上。其固化物有較高的耐熱性。常用的有鄰苯二甲酐。
③ 聚酰胺固化劑 聚酰胺用量多時制品韌性好,耐沖擊;但耐熱性差。用量少時制品耐熱性高,耐腐蝕性好。
④ 酚醛樹脂固化劑 液體酚醛樹脂和粉狀酚醛樹脂都可以做環氧樹脂的固化劑。用酚醛樹脂固化的制品機械強度好,耐熱性好,使用方便,是較好的固化劑。
(4)環氧樹脂的稀釋劑和增塑劑 為改善環氧樹脂的某些性能需要添加一些輔助材料,主要有稀釋劑和增塑劑。
① 稀釋劑有活性稀釋劑和非活性稀釋劑。常用的非活性性稀釋劑有丙酮、二甲苯、香蕉水等。活性稀釋劑有501#活性稀釋劑、609#活性稀釋劑、環氧辛烷等。非活性稀釋劑能與樹脂互溶,將樹脂的粘度降下來,但不參加反應,硬化過程大部揮發掉,降低制品的密度,增加收縮,殘留部分也使機械強度有所降低。活性稀釋劑除有降低樹脂粘度的作用外在硬化過程中還參加固化反應,成為樹脂的組成部分,因而制品的收縮小。使用活性稀釋劑時固化劑用量要略有增加。
② 增塑劑 增塑劑也稱增韌劑能降低環氧樹脂的脆性,常用的非活性增塑劑有鄰苯二甲酸二丁酯,磷酸三乙酯等。活性增塑劑有聚酰胺樹脂、環氧酯、聚硫橡膠等。
非活性增塑劑在磨具制造中常用鄰苯二甲酸二丁酯,它不參加固化反應但能增加樹脂的柔韌性,同時降低樹脂的粘度既起增塑作用也起稀釋作用,但樹脂的抗拉強度有所下降。活性增塑劑能參加固化反應,常用的聚酰胺樹脂既是增塑劑又是固化劑,能使樹脂的抗彎強度和抗沖擊強度有所提高。
3、環氧樹脂在磨具制造中的應用
(1)作酚醛樹脂磨具的潤濕劑 粉狀酚醛樹脂型料易結塊,使用環氧樹脂作潤濕劑,可減少型料結塊,提高松散性。環氧樹脂與酚醛樹脂發生反應固化時減少發泡廢品,還可以提高制品的拋光性能。用于細粒度磨具有很好的效果。
(2)用于制造石墨拋光砂輪和磨轉子槽砂輪都有較好效果。
(3)用于高速磨片和切斷砂輪可減少使用中產生燒傷現象。
(4)用環氧樹脂生產澆注制品如珩磨輪。
三、新酚樹脂(XYLOK)
新酚樹脂是由對苯二甲醇或對苯二甲醚與苯酚在催化劑作用下縮聚而成。為紅褐色固體,比重1.6-1.7,軟化點65℃-105℃,能溶于乙醇、丙酮等有機溶劑。
(1)新酚樹脂的特點 新酚樹脂粘結力強,化學穩定性好,耐熱性能高,硬化時收縮小,制品尺寸穩定。粘結強度比酚醛樹脂提高20%以上,耐熱性提高10℃-20℃。新酚樹脂制品可在250℃以下長期使用,制品耐濕耐堿。
(2)新酚樹脂的硬化 烏洛托品可作新酚樹脂的硬化劑,加入6-10%的烏洛托品在160℃-180℃的溫度下可固化成不溶不熔的固體。用烏洛托品固化的制品耐熱性較好。
(3)新酚樹脂的應用 新酚樹脂與酚醛樹脂按1 :3混合使用不僅提高了酚醛樹脂的強度,還提高了耐熱性和磨削比。在生產工藝上使用熱壓較冷壓制品強度高出約5%-30%,磨削效果也有提高。目前新酚樹脂主要用于重負荷荒磨砂輪和金剛石砂輪。
四、聚胺基雙馬來酰亞胺樹脂(PABM)
PABM樹脂為淡黃色固體,比重1.28-1.30,熔點142-162℃,溶于甲苯、二甲苯等溶劑。
(1)PABM 樹脂的特點 PABM樹脂具有較高的機械強度,具有優良的耐熱性,可在250℃以下長期使用。硬化過程不需另加固化劑,硬化時間短,較酚醛樹脂約減少一半硬化時間,硬化溫度為200℃-240℃。
(2)PABM樹脂的應用 用于制造金剛石砂輪提高耐用度。用于制造磨螺紋砂輪,其尖角保持好。
PABM樹脂應用的并不普遍,主要是價格高,并且沒有高性能的潤濕劑,因而影響了他的適用范圍。
五、聚乙烯醇縮醛(PVA)
聚乙烯醇是由聚乙酸乙烯酯經醇解而制成的,為白色無味粉末,比重1.2-1.3,溶于熱水,耐有機溶劑。
將聚乙烯醇溶于熱水制成15-20%濃度的水溶液與磨料混合,然后加入甲醛水溶液及催化劑鹽酸,充分攪拌后澆注到模具中,在60-80℃的溫度下反應8-10小時,經水洗除酸干燥后即成拋光磨具。成品帶有大量氣孔,富于彈性。可用于拋光不銹鋼、銅、鋁等金屬材料。也用于塑料、皮革等非金屬材料的加工。但生產過程中水洗除酸,污染環境。
§4 輔助材料
常用的輔助材料有填充劑、潤濕劑、增塑劑、稀釋劑、偶聯劑和補強材料。
一、填充劑 有粉狀材料和顆粒狀材料兩種,石膏、螢石等是粉狀材料、萘粒、氧化鋁空心球等屬顆粒狀材料。
(1)半水石膏 CaSO4? H2O,比重2.3,用量1.5-6%。有明顯的補強作用,能降低型料粘性、縮短硬化時間,減少起泡廢品。用量大時制品吸水率增加,耐水性降低。石膏粉技術條件,見表3。

(2)冰晶石 Na3AlF6,比重2.95-3.01,用量1.5-5%,冰晶石熔點較低,可降低磨削熱,增強自銳性,防止砂輪堵塞,提高砂輪強度。冰晶石的技術條件見表4。

(3)石墨粉 主要用于拋光和導電磨削,要求粒度細,純度高。高級鏡面磨砂輪使用膠體石墨。石墨的技術條件見表5。
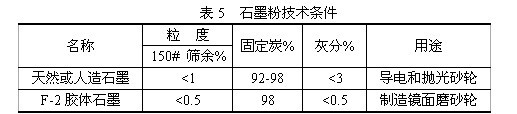
(4)硫化鐵 FeS2,比重5,加入量1.5-3%,用于磨削不銹鋼,可提高磨削效果。
(5)氧化鐵 Fe2O3,比重5.2,加入量1.5-5%,氧化鐵具有補強作用,提高磨具的耐熱性,并有染色作用。
(6)螢石 CaF2,比重3.01-3.25,加入量5-10%,在磨削熱作用下可以分解,增加磨具的自銳性,減少燒傷,提高效率。
(7)炭黑 C,比重1.8-2.1,加入量0.3-3%。
(8)銅粉 Cu,比重8.9,加入量20-50%,銅粉能增加導電能力,用于制造電解磨削用磨輪。
(9)萘粒、塑料顆粒、空心氧化鋁 這類填料都是用于造成磨具中的氣孔,在磨削時起散熱排屑作用。
二、潤濕劑 主要有酚醛樹脂液、液體環氧樹脂、糠醛、乙醇、糖水、機油等,機油能降低制品強度。
三、增塑劑 常用鄰苯二甲酸二丁脂也用低聚酰胺、液體橡膠等作增塑劑,因其還能提高韌性,也稱作增韌劑。
四、稀釋劑 常用的稀釋劑有乙醇、丙酮、二甲苯等。稀釋劑大多在硬化加熱時揮發,易引起制品起泡,應盡量少用。
五、偶聯劑 能聯結結合劑和被粘結物,提高粘結強度。常用的牌號有南大42#,A-151#,A-187#,A-189#等,但用在砂輪上的明顯效果尚待考察。
六、纖維材料 主要起補強作用,常用玻璃纖維網格布,網格布的抗拉強度、耐熱性、彈性和化學穩定性都很好。
(1)玻璃纖維網格布 磨具制造使低堿或有堿玻璃纖維網格布,因無堿產品成本較高。
磨具中用的網格布一般為45-60支加捻紗(支為1g纖維長的米數)。薄片砂輪可選10-30股紗,4-6目的網格布。一般砂輪選用20-40股紗,6-8目的網格布。網格布表面涂有酚醛樹脂或環氧樹脂等,以增加與制品的粘結性。但網格布存放時間過長時,則樹脂變硬,失去柔韌性,影響與制品的粘結。
(2)短纖維 有的制品將切短的玻璃纖維或金屬纖維直接在混料時加入型料中也有很好的補強效果。
七、金屬材料 在制造重負荷荒磨砂輪時內部都加2-3只鋼環,以增加強度,孔部有時也加金屬保徑圈,使強度有很大提高。
§5 樹脂磨具的配方
樹脂磨具的配方主要由磨料、潤濕劑、結合劑和填料等組成并給出成型密度。如A80#磨具配方:
A80# 100
酚醛潤濕劑 3
酚醛樹脂粉 7
石膏粉 3
成型密度 2.31g/cm3
1、磨具硬度的調節
提高磨具硬度主要是增加結合劑量和提高成型密度。在同材質同粒度的配方中結合劑增加0.8-1.5份,成型密度增加0.02-0.05 g/cm3,可以增加一級硬度。
2、提高磨具強度
(1)增加結合劑量 提高成型密度,使用混合粒度磨料,都可提高磨具強度。
(2)加入適當的填充劑或玻璃纖維等。
(3)使用偶聯劑(效果不甚明顯)。
(4)對磨料進行凈化處理;酸堿洗、水洗;煅燒。
(5)在磨具內加入玻璃纖維網格布,或金屬環。
(6)成型時加大孔部密度,或孔部使用細號的磨料。
§6 樹脂磨具的配混料
按配方算出投料量并增加消耗量,打制施工票,配料并混合型料。
一、混料的基本原則
(1)混料車間最好恒溫,達不到恒溫要求的,室溫高用粘度高的潤濕劑,粉狀樹脂的軟化點也可以高一些,反之亦然。
(2)磨料粒度粗潤濕劑粘度高些,粒度低粘度低些。
(3)磨料與潤濕劑要混均勻,加入粉狀樹脂和填料后要迅速混均出料,不及時混均則易結塊。
(4)加入粉狀樹脂和填料時要過篩,均勻加入。
二、混料工藝流程
(1)粗粒度樹脂磨具的混料工藝流程見圖3。
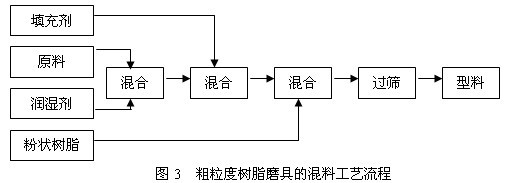
(2)細粒度樹脂磨具的混料工藝流程見圖4。
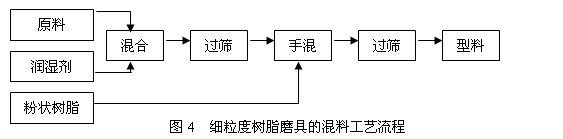
三、混料過程的調整
1、型料過濕
(1)改用高粘度的潤濕劑。
(2)增加粉狀樹脂用量,減少液體樹脂用量。
(3)使用干料;干料是混過液體樹脂干燥后篩松的料,使用的樹脂量要計入結合劑中。
(4)增加石膏粉用量,操作者允許調整量不超過配方規定量的1/3。
2、型料過干
(1)使用粘度低的潤濕劑。
(2)加入少量溶液。
(3)增加液體樹脂用量,相應的減少粉狀樹脂用量。
(4)減少石膏粉用量,操作者允許調整量不超過配方規定量的1/3。
四、混料時間及過篩的要求
(1)混料時間要適當,如時間太短則混合不均,時間太長則易發熱而是料發粘結塊。當磨料粒度細,樹脂量大時混料時間需稍長。
(2)型料過篩不僅是消除結塊,也是使型料混合均勻的重要方法。尤其是細粒度型料潤濕劑混合過程和加入粉狀樹脂后的混合都應當輔以1-2次的過篩,隨著磨料粒度的不同篩號也有粗細的變化。可參考的混料時間和過篩篩號,見表6。

§7 樹脂磨具的成型
一、高速磨片和切斷砂輪的成型
高速磨片和切斷砂輪多采取冷壓成型或低溫熱壓成型,低溫熱壓溫度在80℃左右,脫模后再進爐硬化。熱壓制品較冷壓制品密度大強度高,與網格布和保徑環結合的好。高速磨片和切斷砂輪的成型工藝流程,見圖5。

二、細粒度磨具的熱壓成型
粒度細硬度高的制品如小螺距磨螺紋砂輪等采取干粉料熱壓。將磨料和粉狀樹脂在球磨機中混合,球料比為1:1,混合30分鐘左右,過20#篩,即為干粉狀型料。將模具預熱至50℃~60℃,涂脫模劑后,投料、括平、熱壓。熱壓溫度185℃。保壓時間為每毫米厚的制品保壓2~3分鐘。熱壓中間可放氣1~2次。熱壓完成后冷卻至100℃左右可卸模。細粒度磨具熱壓工藝流程見圖6
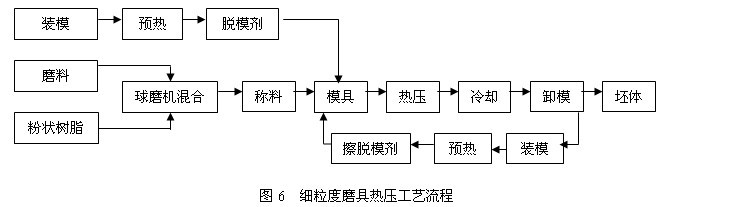
三、重負荷荒磨砂輪熱壓成型
重負荷砂輪用新酚樹脂與酚醛樹脂以1:3的比例混合作結合劑,磨料用10#~20#鋯剛玉,燒結剛玉或代以微晶棕剛玉熱壓成型,制件密度達到2.9~3.2g/cm3,孔部加入兩只鋼環增強。
重負荷砂輪結合劑用量比較大,達50%,常先冷壓成型預干燥后再回模熱壓成型,熱壓溫度120℃~140℃,熱壓中排氣數次,保壓一小時,冷卻至60℃以下脫模,坯體經40小時固化,最高溫度為185℃,保溫4小時。重負荷砂輪熱壓工藝流程見圖7。

制造衍磨輪和PVA拋光輪采取澆注成型。衍磨輪以環氧樹脂作為粘結劑,乙二胺作為固化劑,冷硬化。
§8 樹脂磨具的硬化與加工
樹脂磨具硬化過程中,溫度由室溫升高后揮發物(包括水分)從磨具中揮發,如升溫過快易起泡。粉狀樹脂也在升溫過程中軟化,磨具坯體強度降低,異形和厚度高、尺寸大的砂輪易變形、倒塌。樹脂磨具硬化的最終溫度為180℃~190℃,經一段保溫時間后可冷卻出爐。
制品硬化后成深褐色,硬化不足呈黃綠色,過硬化則炭化,變黑。
一、硬化設備
1、電加熱
(1)電烘箱 為小型成品設備,作為實驗用比較方便。容積約0.1~0.3m3 。
(2)熱風爐 電加熱,熱風循環,容積約2~3m3
(3)紅外線硬化爐 結構與熱風爐近似,但建成隧道結構,長5~30m,分預熱帶、加熱帶、冷卻帶、功率20~150KVA。為連續性生產,產量比較高。
2、煤氣加熱 實際就是煤氣加熱的熱風爐,如其結構設計合理,使用效果也較好。
3、干燥室 有些制品硬化前先預干燥,可減少制品發泡變形,縮短硬化時間。構成多為燒煤的室式結構,也有是合理利用余熱的,依現場條件而定。干燥溫度為80℃~110℃,干燥時間約8小時。
二、裝爐方式
1、敞開法 將砂輪平放在托板上硬化。這種方法容易造成上下兩面硬度不均。為使揮發物順利排出,托板多制成帶孔槽的結構,或使用耐火物、廢切斷砂輪等作托板。
2、加蓋法 裝爐時在制件上端蓋上墊板,使坯體上下面受熱盡量一致。對高速磨片還可在上蓋上面加彈簧壓緊;對切斷砂輪增加上蓋板的重量都有較好的硬化效果。
3、埋砂、圍紙法 對于異形砂輪為防止硬化時變形,可埋入石英砂硬化,但因不與熱空氣直接接觸,往往制品顏色欠佳。對于薄壁的筒形砂輪可在硬化時用牛皮紙圍住,防止倒塌、變形。
三、硬化方法和曲線
1、硬化方法 對不易發泡變形的制品可采取不經過干燥工序直接硬化。而粒度細、硬度高、易發泡的制品則要增加預干燥工序,干燥溫度80℃左右。粒度細、硬度高、規格大的制品還可用加壓硬化罐,硬化升溫的同時給予8~12個大氣壓力的壓縮空氣。個別產品還可采取帶模硬化,但所占爐內容積大,操作笨重不便,一般不用。
2、硬化曲線 酚醛樹脂制品硬化溫度一般在185℃左右,環氧樹脂制品可降低20℃左右的硬化溫度,視具體情況而定。
硬化時間按制品大小、硬度高低與粒度的粗細而定。總的硬化時間在10~40小時之間,升溫時間和最高溫度保溫時間如式(3),(4)

T——總的硬化時間(小時)
B——最高溫度保持時間(小時)
S——升溫時間(小時)
在升溫過程中在80℃左右和110℃左右可安排一些保溫時間,通常在2~3小時之間,以利于揮發物排出。
四、樹脂磨具的加工 樹脂磨具的加工設備、加工方法基本上與陶瓷磨具的加工相似。一般切斷砂輪和鈸型砂輪硬化后不再加工。