摘要 一、主題內容與適用范圍本標準規定了用于冶金脫氧劑和耐火材料的出口碳化硅中碳化硅含量的分析方法。本標準適用于出口
一、主題內容與適用范圍
本標準規定了用于冶金脫氧劑和耐火材料的出口碳化硅中碳化硅含量的分析方法。
本標準適用于出口中、低品位碳化硅的測定,磨料級碳化硅也可參照使用。
二、引用標準
GB1.4 標準化工作導則 化學分析方法標準編寫規定
GB1467 冶金產品化學分析方法標準的總則及一般規定
三、試樣的制備
(一)塊狀試樣
先用錘子于鋼板上將大塊打碎至所有樣品都通過2.5mm篩,充分混合后,分取1kg樣品;利用對輥粉碎機使樣品全部過1mm篩,分取約100g試樣,吸鐵;用鋼乳缽將樣品粉碎至全部過100目篩,分取約25g樣品,用磁鐵吸出粉碎時帶入的鐵屑,放入稱量瓶中,在105±5℃的烘箱中干燥1h,取出置于干燥器中冷卻備用。
(二)粒狀試樣
將樣品混合均勻,分取約100g試樣,按3.1相同步驟,使樣品全部過100目篩,分取約25g,吸鐵,烘干,置于干燥器中冷卻備用。
四、碳化硅含量的測定
(一)燃燒-重量法(方法一)
1.方法提要
試樣置于高溫爐內在一定溫度下灼燒,除去游離碳后,稱取灼燒后殘渣,加助熔劑在氧氣流中高溫加熱,分解使碳化硅中的碳完全燃燒生成二氧化碳,二氧化碳用裝有堿石棉及高氯酸鎂的吸收瓶吸收,根據吸收瓶的增重來計算含碳量,換算為碳化硅的含量。
2.試劑及儀器裝置
(1)氧氣,99.5%以上。
(2)助熔劑,稱取45g分析純四氧化三鉛及7g三氧化二硼于素瓷皿中,在950℃加熱熔化約5min,取出,將熔液立即倒在鋁質皿內或板上,冷卻后用瓷研缽將其研成細顆粒備用。
(3)堿石棉,化學純,粒度為20~30目。
(4)無水高氮酸鎂,粒度為24~50目。
(5)偏釩酸銀或活性二氧化錳(顆粒狀)。
(6)箱式高溫爐。
(7)管式高溫爐。
測定碳的裝置及二氧化碳吸收瓶詳解圖如圖1、圖2所示。
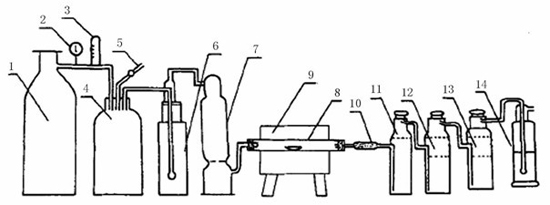
圖1燃燒—重量法測定碳裝置
1—氧氣鋼瓶;2—氣壓表;3—流量計;4—緩沖瓶;5—通氣閥;6—洗氣瓶;
7—干燥塔;內裝1/2堿石棉及1/2高氯酸鎂;8—燃燒管;9—管式爐;10—脫硫管:內裝活性二氧化錳或偏釩酸銀;11—干燥塔:內裝高氯酸鎂;12,13—二氧化碳吸收瓶、內裝2/3堿石棉及1/3高氯酸鎂;14—濃硫酸干燥瓶
7—干燥塔;內裝1/2堿石棉及1/2高氯酸鎂;8—燃燒管;9—管式爐;10—脫硫管:內裝活性二氧化錳或偏釩酸銀;11—干燥塔:內裝高氯酸鎂;12,13—二氧化碳吸收瓶、內裝2/3堿石棉及1/3高氯酸鎂;14—濃硫酸干燥瓶

圖2二氧化碳吸收瓶詳解圖
(1)灼燒減量的測定
稱取干燥試樣(3.1或3.2)1g(精確至0.1mg)于灼燒至恒重的方舟內,置于高溫爐中在850±20℃灼燒2h1),取出,在空氣中稍冷卻后,置于干燥器中繼續冷卻至室溫,稱重。殘渣用于結合碳的測定。
灼燒減量按式(1)計算:
MV(%)= ×100 …………………(1)m1-m2m
式中:Mv—灼燒減量,%;
m—試樣重,g;
m1—灼燒前試樣加方舟重,g。
m2—灼燒后試樣加方舟重g。
殘渣百分含量按式(2)計算:

式中:R—殘渣百分含量,%。
注1)當游離碳的含量太高時,可適當延長灼燒時間。
(2)結合碳的測定
結合碳是指與硅化合形成碳化硅的那部分碳。用燃燒—重量法測定碳的裝置如圖1所示。具體測定步驟如下:
(3)空白測定
將爐溫升到1050℃±30℃,通氧氣,調節氧氣流速(氧氣流速以硫酸干燥瓶(14)中不連續冒氣泡為宜),在開始測定前,先灼燒廢樣以清洗氣路,同時檢驗裝置氣密性及氣路是否暢通,然后分別稱取兩吸收瓶重量。
稱取3g助熔劑于預先空燒過的瓷舟中,拔開燃燒管入口塞子,用送樣棒將瓷舟送至燃燒管中央高溫處,迅速塞緊塞子,通氧氣40 min,通氣閥(5)通大氣,拔開燃燒管入口塞子,取出瓷舟,待硫酸干燥瓶(14)內兩液面平行時,迅速關閉吸收瓶,分別稱取兩吸收瓶重量。空白值直接以第一個吸收瓶的增重mo(g)表示。
(4)標樣的測定
稱取0.2g標樣(精確至0.1mg)于預先空燒過的瓷舟內,蓋上3g助熔劑,以下按空白測定(4.1.3.3)相同步驟進行,利用第一個吸收瓶的增重,按公式(3)計算碳含量1)。當測定結果在允差范圍內時,說明裝置正常,可進行試樣測定。
注:1)第二個吸收瓶用來考察吸收瓶的穩定性,每次吸收前后重量變化在士0.5mg范圍內時,視為正常。
(5)試樣的測定
稱取0.2g(精確至0.1mg)測定灼燒減量后的殘渣于瓷舟內,蓋上3g助熔劑,以下按標樣測定相同步驟(4.1.3.4)進行。測定完畢,關閉管式爐及氧氣,將吸收瓶置于干燥器中保存備用。
(6)碳含量的計算
碳的百分含量按公式(3)計算:

式中:Cr—結合碳的百分含量,%;
m—試樣稱取量,g;
m1—吸收前第一吸收瓶重量,g;
m2—吸收后第一吸收瓶重量,g;
m0—空白測定值,g;
0.2729—二氧化碳換算為碳的系數。
4.分析結果的計算
碳化硅的百分含量按公式(4)計算:

式中:SiC碳化硅的百分含量,%;
R—殘渣百分含量,%;
Cr —結合碳的百分含量,%;
3.3384-碳換算為碳化硅的系數。
5.允差及分析結果的取舍
表1允許范圍

驗收試樣分析值程序按附表A(補充件)進行。
(二)焦硫酸鉀法(方法二)
1.方法提要
試樣先經灼燒除盡游離碳,殘渣經氫氟酸揮硅后,加焦硫酸鉀加熱融熔,鹽酸溶解熔塊,過濾洗滌,于800±5℃灼燒至恒重。
2.試劑、儀器及裝置
(1)氫氟酸:分析純。
(2)硫酸溶液:(1+1)。
(3)焦硫酸鉀(或硫酸氫鉀):分析純。
(4)鹽酸溶液:(1+1,5+95)。
(5)高溫爐。
(6)容積為100ml的鉑金皿。
3.測定步驟
(1)稱取試樣3.1或3.2約1g,精確至0.1mg于灼燒至恒重的100ml的鉑金皿內,在800℃灼燒2h。
(2)試樣自然冷卻后,加15~20ml氫氟酸,5~6滴(1十1)硫酸及1ml濃硝酸,置于砂浴上加熱,直至三氧化硫白煙冒盡。
(3)加10g焦硫酸鉀,先在砂浴上加熱1h,烘干表存水。在420℃加熱熔化,并保持5min,將爐溫升至800℃。取出稍冷,加入80ml(1+1)的鹽酸加熱溶解,用中速濾紙趁熱過濾,先用(5十95)的熱鹽酸洗3-4次,再用熱蒸餾水洗數次,然后用蒸餾水洗至無氯離子。濾紙及殘渣置于灼燒至恒重的增竭中,先低溫灰化,然后將爐溫升到800±5℃,灼燒至恒重。
4.碳化硅含量的計算碳化硅的百分含量按式(5)計算:

式中:SiC碳化硅百分含量,%;
m—試樣重,g;
m1—空坩堝重,g;
m2—坩堝及殘渣重,g;
4.允差
表2允差范圍

