摘要: 采用復(fù)合電鍍技術(shù)在炭素結(jié)構(gòu)鋼板的表面上制備高硬度的 Ni- SiC 納米復(fù)合鍍層, 研究鎳- 碳化硅納米復(fù)合電鍍的工藝條件。結(jié)果表明, 當(dāng)陰極電流密度為 2.56 A/dm2, 鍍液中納米碳化硅粉的質(zhì)量濃度為 20 g/L, 鍍液的 pH 值為 5.0, 溫度為 50 ℃時(shí), 鍍層生長良好, 均勻細(xì)致平滑, 鍍層的顯微硬度可達(dá)到 950HV0.2, 遠(yuǎn)高于普通純鎳鍍層的硬度。
關(guān)鍵詞: 納米復(fù)合電鍍; 鎳- 納米碳化硅; 顯微硬度
復(fù)合電鍍技術(shù)是在電鍍液中添加一種或數(shù)種不溶性的固體顆粒, 使其與金屬離子共沉積而形成具有特殊功能鍍層的電鍍技術(shù)。如添加顆粒為納米級(jí)的顆粒,因納米材料的獨(dú)特結(jié)構(gòu)而具有的小尺寸效應(yīng)、量子尺寸效應(yīng)、宏觀量子隧道效應(yīng)及表面和界面效應(yīng)等, 使之具有與傳統(tǒng)材料不同的物理和化學(xué)性質(zhì)[1]。納米金剛石和納米陶瓷粉具有很高的硬度和良好的耐高溫性能, 應(yīng)用在復(fù)合電鍍中能較大幅度地改善鍍層的力學(xué)性能[2]。復(fù)合鍍作為材料表面強(qiáng)化的一種新手段, 因其鍍層具有的高硬度、耐磨性、自潤滑性、耐蝕性、特殊的裝飾外觀以及電接觸、電催化等功能而倍受人們的關(guān)注[3]。
納米顆粒在鍍層中的含量及存在狀態(tài)是影響鍍層性能的關(guān)鍵因素, 如何使得納米顆粒在鍍層中均勻地分散是該技術(shù)的難點(diǎn)。本試驗(yàn)采用復(fù)合電鍍技術(shù)在Q235 炭素結(jié)構(gòu)鋼板的表面上制備了高硬度、高耐磨的Ni- SiC 納米復(fù)合鍍層, 研究電沉積的最佳工藝條件和影響因素, 為實(shí)現(xiàn)工業(yè)化應(yīng)用提供理論和實(shí)驗(yàn)依據(jù)。
1 實(shí)驗(yàn)方法
1.1 實(shí)驗(yàn)儀器及原料
實(shí)驗(yàn)儀器: ZDA01/12 型硅整流設(shè)備, WMK- 03A型溫度控制器, XMT- 102 型數(shù)顯式溫度控制儀, 電動(dòng)可調(diào)速式攪拌器, PHS- 29A 型數(shù)字酸度計(jì), 自制電鍍槽, HXD- 1000TC 顯微硬度計(jì)。
實(shí)驗(yàn)原料: 硫酸鎳, 硫酸鈷, 硼酸, 氯化鎳, 硫酸, 鹽酸, 氫氧化鈉, 復(fù)配表面活性劑, 自制 CYJ- 8 專用除油劑。納米碳化硅粉(平均粒徑為 50~70 nm), Q235 炭素結(jié)構(gòu)鋼板(試件), 所用化學(xué)試劑均為分析純。
1.2 復(fù)合電鍍工藝流程
試件電鍍工藝流程為: 試樣→磨光→化學(xué)除油→水洗→除銹→水洗→電解除油→水洗→活化→復(fù)合電鍍→水洗→晾干。
1.2.1 除油
試件的除油分為化學(xué)除油和電解除油兩個(gè)部分。試件的表面在以前的加工處理過程中, 為了防止試件生銹和方便保存, 在其表面涂了一層油脂物質(zhì), 為了保證鍍層與試件的結(jié)合力, 需對(duì)試件進(jìn)行除油處理。
首先是化學(xué)除油, 除油溶液由自制的 CYJ- 8 專用除油劑按質(zhì)量濃度為 70~80 g/L 配制而成。把打磨好的試件放進(jìn)盛有除油溶液的大燒杯中, 攪拌并加熱至除油溶液沸騰 5~6 min。然后是電解除油, 電解除油所用除油液與化學(xué)除油溶液相同, 首先把除油液加熱到40 ℃恒溫, 然后把化學(xué)除油后經(jīng)水洗的試件放在電解除油液中, 通電并調(diào)節(jié)電流大小為 2 A, 先將試件做陰極, 陽極用大鐵片, 除油 2 min。然后將試件做陽極, 陰極用大鐵片, 除油 1 min。金屬制品在溶液中受電流作用而發(fā)生極化, 使金屬制品表面和堿性溶液間的界面張力降低, 使除油液對(duì)金屬表面的潤濕性增強(qiáng)。同時(shí)陰極和陽極產(chǎn)生的氣體也有利于油膜的破裂, 從而使除油過程進(jìn)一步強(qiáng)化。
1.2.2 化學(xué)除銹
將金屬試件浸入較高濃度和一定溫度的侵蝕液中以除去制品上的氧化物和銹蝕產(chǎn)物。將除油水洗后的試件放在質(zhì)量分?jǐn)?shù)為 18%的鹽酸溶液中。為加快除銹速度, 可把鹽酸溶液適當(dāng)加熱, 但不要太熱, 否則易使鹽酸揮發(fā)出來, 產(chǎn)生大量的刺激性氣味, 一般以 40 ℃為宜, 直至試件上的銹除完為止。
1.2.3 活化(弱侵蝕)
在試件進(jìn)行電鍍之前要進(jìn)行活化處理, 以除去金屬表面的極薄氧化膜, 使金屬表面活化以保證鍍層與基體金屬結(jié)合牢固。把試件放在質(zhì)量分?jǐn)?shù)為 5%的稀鹽酸中 1 min, 然后放在大約 50 ℃的水中清洗, 再用冷水清洗干凈。對(duì)清洗完的試件, 應(yīng)立即實(shí)施電鍍。
1.2.4 復(fù)合電鍍
電鍍陽極為純鎳板, 電鍍陰極為 1 mm×28 mm×100 mm Q235 炭素結(jié)構(gòu)鋼板。
鍍液的組成(以下均為質(zhì)量濃度):硫酸鎳為 270 g/L,硫酸鈷為 12 g/L, 硼酸為 35 g/L, 氯化鎳為 15 g/L, 復(fù)配表面活性劑為 0.85 g/L, 納米碳化硅粉適量。電流密度2.56 A/dm2, 鍍液的 pH 為 5.0, 鍍液的溫度為 50 ℃。電鍍時(shí)間為 20 min。
由于納米材料尺寸小其活性高, 在鍍液中易團(tuán)聚,所以, 納米 SiC 的分散問題是納米復(fù)合電鍍的關(guān)鍵。在施鍍之前, 須對(duì)其進(jìn)行有效分散, 本試驗(yàn)先采用復(fù)配表面活性劑對(duì)納米 SiC 進(jìn)行潤濕和分散, 再在超聲波中振蕩 30 min, 利用超聲波的空化效應(yīng)和機(jī)械剪切作用能有效地?cái)嚢韬头稚⒓{米 SiC。實(shí)驗(yàn)表明, 經(jīng)分散處理過的納米 SiC 在鍍液中呈懸浮狀態(tài), 要經(jīng)過較長時(shí)間的靜置才能完全沉淀下來, 證實(shí)了此方法分散納米SiC 的有效性。
1.3 復(fù)合鍍層的檢測
用 HXD- 1000TC 顯微硬度計(jì)進(jìn)行復(fù)合鍍層顯微硬度的測定(HV), 試驗(yàn)力為 1.961 N, 保持時(shí)間為 15 s,每個(gè)試樣測試 5 次, 取其平均值。
2 結(jié)果與討論
固體顆粒進(jìn)入鍍層中, 即金屬與固體顆粒共沉積的機(jī)理問題到目前還沒有一個(gè)完善、統(tǒng)一的理論。目前, 國內(nèi)外比較流行的有以下兩類理論: ①在復(fù)合電鍍過程中, 力學(xué)作用起主要作用, 同時(shí)陰極電流效率和鍍液的微觀分散能力也是重要影響因素。通過攪拌使得鍍液中的微粒很好地懸浮起來, 給微粒和陰極的相互接觸創(chuàng)造條件, 而當(dāng)微粒停留在陰極表面, 就有可能被電沉積的金屬嵌入鍍層中。②荷電的微粒在電場的作用下的電泳遷移速度是微粒進(jìn)入復(fù)合鍍層的關(guān)鍵因素。這是因?yàn)楸M管微粒的電泳速度要比攪拌引起的微粒隨著液流的遷移速度小得多, 但在微粒到達(dá)陰極界面的分散雙層后, 由于電位差的影響, 在界面間產(chǎn)生極高場強(qiáng), 電泳速度變大, 微粒以垂直于電極表面的方向向陰極移動(dòng), 并被金屬嵌入鍍層。
本試驗(yàn)研究了金屬鎳- 碳化硅納米復(fù)合電鍍的工藝條件, 討論了各工藝條件對(duì)鍍層外觀及硬度的影響。
2.1 陰極電流密度對(duì)鍍層的影響
在鍍液的 pH 值為 5.0, 溫度為 50 ℃, 納米碳化硅的質(zhì)量濃度為 20 g/L 的條件下, 考察陰極電流密度對(duì)鍍層的影響, 試驗(yàn)結(jié)果見表 1。
電流密度較高時(shí), 鍍液中的離子和納米 SiC 微粒遷移速度快, 導(dǎo)致在陰極上形成不規(guī)則的排列, 沉積過程紊亂、無序, 鍍層密度低, 表面粗糙。同時(shí)沉積速度快還會(huì)導(dǎo)致鍍層的內(nèi)應(yīng)力增大, 使鍍層開裂或剝落。
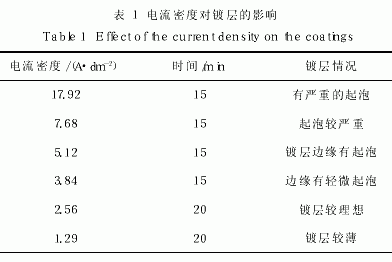
由表 1 可知, 電流密度較大時(shí), 試件上使鍍層邊緣部分和基體金屬結(jié)合不好, 產(chǎn)生起泡現(xiàn)象。當(dāng)電流密度為 2.56 A/d㎡時(shí), 鍍層有很好的效果。故電鍍合適的陰極電流密度為 2.56 A/d㎡。
2.2 鍍液中納米碳化硅的加入量對(duì)鍍層的影響
鍍液中納米碳化硅的加入量影響鍍層中納米碳化硅的共沉積量, 從而直接影響著鍍層的硬度。選擇鍍液溫度為 50 ℃, pH 值為 5.0, 陰極電流密度為 2.56 A/d㎡,時(shí)間為 20 min, 改變鍍液中納米碳化硅的含量, 分別測量鍍層的顯微硬度, 實(shí)驗(yàn)結(jié)果如圖 1 所示。
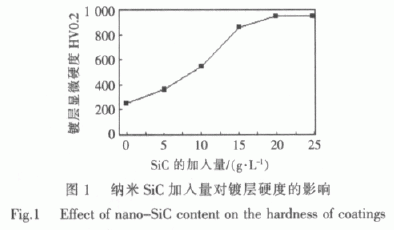
實(shí)驗(yàn)結(jié)果表明, 改變鍍液中納米碳化硅的質(zhì)量濃度, 鍍層硬度隨納米碳化硅的質(zhì)量濃度的增加而增加。在碳化硅的質(zhì)量濃度為 20 g/L 時(shí)硬度最大。這表明鍍液中粒子的質(zhì)量濃度愈大, 輸送到陰極表面的顆粒愈多, 嵌入鍍層的的幾率愈大, 鍍層的性能愈好。但粒子的質(zhì)量濃度有一個(gè)臨界值, 即 CSiC=20 g/L, 再增大加入量, 鍍層硬度不再增大。這是因?yàn)殄円褐形⒘5暮窟_(dá)到一定值后, 微粒在鍍液中的無規(guī)則運(yùn)動(dòng)就會(huì)阻礙金屬離子向陰極的定向移動(dòng), 從而使鍍層中微粒的含量不再增大[4]。
2.3 鍍液 pH 值對(duì)鍍層性能的影響
在鍍液溫度為 50 ℃, 納米碳化硅的質(zhì)量濃度為20 g/L, 陰極電流密度為 2.56 A/d㎡, 時(shí)間為 20 min時(shí), 考察鍍液 pH 值對(duì)鍍層質(zhì)量的影響, 結(jié)果見表 2。
H+和 OH- 能夠改變 SiC 微粒的電荷性能。H+吸附于微粒表面, 使其在電場力作用下向陰極移動(dòng), 有利于共沉積的進(jìn)行。而 pH 太小所引起的陰極析氫又對(duì)微粒在陰極表面的吸附有不利影響。pH 值過大時(shí), 可以
在陰極附近產(chǎn)生高度分散的鎳的氫氧化物, 鎳離子的質(zhì)量濃度降低。因此鍍液的 pH 值對(duì)鍍層的生長有較大影響。由表 2 實(shí)驗(yàn)結(jié)果可知, 當(dāng) pH 值為 5.0 時(shí), 鍍層生長良好, 表面均勻細(xì)致、質(zhì)量最好。
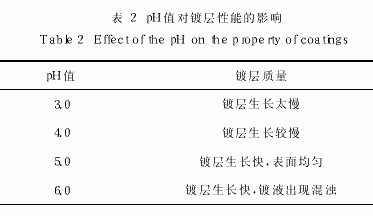
2.4 鍍液溫度對(duì)鍍層性能的影響
在鍍液中碳化硅的質(zhì)量濃度為 20 g/L, pH 值為5.0, 陰極電流密度為 2.56 A/d㎡, 時(shí)間為 20 min 時(shí), 考察溫度對(duì)鍍層性能的影響, 結(jié)果見表 3。
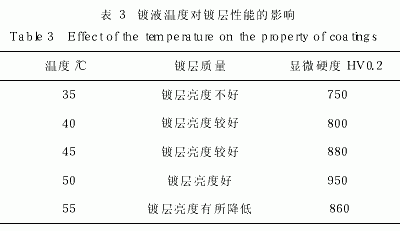
由表 3 可知, 在復(fù)合電鍍過程中, 隨著鍍液溫度的升高, 鍍層的外觀和硬度有一定程度的改善和升高, 但達(dá)到一定值后又有所降低。當(dāng)溫度為 50℃時(shí), 鍍層的亮度最佳。硬度也達(dá)到最大值, 這是因?yàn)樵陔姵练e過程中升高溫度, 將使鍍液中粒子的熱運(yùn)動(dòng)加強(qiáng), 增加了其的動(dòng)能, 促進(jìn)了粒子向陰極表面的輸送, 有利于納米微粒的復(fù)合電沉積, 鍍層中微粒的共沉積量的增加使鍍層的硬度增加。但是當(dāng)溫度增大到一定值時(shí), 由于鍍液中離子的平均動(dòng)能較大, 會(huì)導(dǎo)致納米微粒表面對(duì)溶液中陽離子的吸附能力降低, 難以吸附在陰極表面, 從而不利于基質(zhì)金屬和微粒的共沉積[4]。
3 結(jié) 論
采用納米復(fù)合電鍍技術(shù)制備 Ni- SiC 納米復(fù)合鍍層, 陰極電流密度、鍍液中納米微粒的質(zhì)量濃度、鍍液的 pH 值和溫度對(duì)鍍層的外觀和硬度都有影響。研究表明, 當(dāng)陰極電流密度為 2.56 A/dm2, 鍍液中納米 SiC的質(zhì)量濃度為 20 g/L, 鍍液的 pH 為 5.0 和溫度為 50 ℃時(shí), 所得到的納米復(fù)合鍍層均勻細(xì)致平滑, 表面光亮,鍍層的顯微硬度可達(dá)到 950HV0.2, 遠(yuǎn)高于普通純鎳鍍層的硬度。
參考文獻(xiàn):
[1] 張立德, 牟季美.納米材料和納米結(jié)構(gòu)[M].北京: 科學(xué)出版社, 2001: 433- 439.
[2] 徐龍?zhí)茫?周美玲.含納米粉鍍液的電刷鍍復(fù)合鍍層試驗(yàn)研究[J].中國表面工程, 1999, 3: 7- 11.
[3] 張勝濤.電鍍工程[M].北京: 化學(xué)工業(yè)出版社, 2002: 296-313.
[4] 馮秋元, 李廷舉, 金俊澤.影響微粒復(fù)合沉積的諸因素[J].材料保護(hù), 2006, 39(5) : 35- 39.